Method for reducing calcium-sulfur ratio in nid semi-dry desulfurization process
A technology of semi-dry desulfurization and calcium-sulfur ratio, applied in the field of flue gas desulfurization, can solve the problems of seldom involving NID semi-dry desulfurization process, high cost of desulfurization, difficult resource utilization of desulfurization ash, etc., to reduce secondary Effects of pollution, production reduction, and consumption reduction
- Summary
- Abstract
- Description
- Claims
- Application Information
AI Technical Summary
Problems solved by technology
Method used
Image
Examples
Embodiment 1
[0029] Contains SO 2 Concentration is 1800m g / m 3 , the flue gas volume is 500,000 m 3 The flue gas per hour enters the desulfurization reactor and desulfurizes with quicklime and circulating ash added with humidifying water in the reactor. Among them, the flue gas inlet temperature (reactor inlet temperature) is controlled to be 130°C, and the humidifying water temperature is 25°C, the water-cement ratio is set to 3%; and by adjusting the setting of the outlet temperature of the reactor, the flue gas outlet temperature is close to and slightly higher than the dew point temperature by 5-15°C, and the dew point temperature value is calculated by formula (1) Furthermore, it is preferable to control the flue gas outlet temperature to 88°C to prevent the corrosion of the equipment caused by flue gas condensation. At the same time, after the flue gas outlet temperature is lowered, the desulfurization efficiency will gradually increase. At this time, the setting of the calcium-su...
Embodiment 2
[0032] Contains SO 2 The concentration is 1800mg / m 3 , the flue gas volume is 500,000 m 3 The flue gas per hour enters the desulfurization reactor and desulfurizes with quicklime and circulating ash added with humidifying water in the reactor. Among them, the flue gas outlet temperature is controlled at 93°C, the humidifying water temperature is 25°C, and the water-cement ratio is set It is set at 3%, and the flue gas inlet temperature is controlled at 135°C. The flue gas inlet temperature is realized by controlling the parameters of the sintering process, such as: by reducing the machine speed, reducing the air leakage rate of the equipment, increasing the temperature of the mixture, and improving the cloth Effects and other measures can increase the flue gas inlet temperature of the desulfurization system. After the flue gas inlet temperature is adjusted, the desulfurization efficiency will gradually increase. At this time, the setting of the calcium-sulfur ratio can be app...
Embodiment 3
[0035] Contains SO 2 The concentration is 1800mg / m 3 , the flue gas volume is 500,000 m 3The flue gas per hour enters the desulfurization reactor and performs desulfurization reaction with quicklime and circulating ash added with humidifying water in the reactor. The flue gas inlet temperature is controlled at 130°C, the flue gas outlet temperature is 93°C, and the water-cement ratio Set it to 3%, and increase the temperature of the humidifying water to 50-75°C, preferably 50°C by raising the temperature of the humidifying water from normal temperature water or replacing the normal temperature water with equipment cooling water. At the same time, the desulfurization efficiency will gradually increase after the temperature increases At this time, the setting of the calcium-sulfur ratio can be appropriately lowered. When setting, pay attention to the change of the desulfurization efficiency while setting, so as to ensure that the outlet flue gas SO 2 The concentration reaches ...
PUM
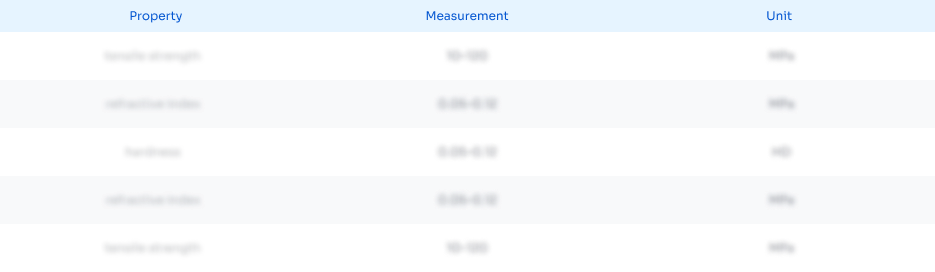
Abstract
Description
Claims
Application Information

- Generate Ideas
- Intellectual Property
- Life Sciences
- Materials
- Tech Scout
- Unparalleled Data Quality
- Higher Quality Content
- 60% Fewer Hallucinations
Browse by: Latest US Patents, China's latest patents, Technical Efficacy Thesaurus, Application Domain, Technology Topic, Popular Technical Reports.
© 2025 PatSnap. All rights reserved.Legal|Privacy policy|Modern Slavery Act Transparency Statement|Sitemap|About US| Contact US: help@patsnap.com