Permanent magnet adjuster
A permanent magnet governor, permanent magnet technology, applied in electrical components, electromechanical devices, electromechanical transmission devices, etc., can solve the problems of many fault points, electromagnetic interference, short life cycle, etc., to achieve controllable output torque and speed, Avoid axial thrust, simple installation and debugging
- Summary
- Abstract
- Description
- Claims
- Application Information
AI Technical Summary
Problems solved by technology
Method used
Image
Examples
Embodiment 1
[0018] Such as figure 1 As shown, the present invention includes: a split and coaxial first shaft 1 and a second shaft, characterized in that: the first shaft 1 is fitted with an annular permanent magnetic turntable 4, and A ring-shaped bushing 15 is set on the bushing 15, and a ring-shaped conductor turntable 10 is set on the bushing 15. Two coaxial cylindrical protrusions are fixedly connected to the outer edge of the permanent magnet turntable 4: that is, away from the first The outer magnetic cylinder 6 of a shaft 1 and the inner magnetic cylinder 9 close to the first axis 1, a circle of permanent magnets 8 are installed on the outer surface of the inner magnetic cylinder 9 and the inner surface of the outer magnetic cylinder 6, and the inner magnetic At the position corresponding to the surface of the magnetic cylinder 9 and the outer magnetic cylinder 6, the magnetic poles of the permanent magnet 8 are opposite; the outer edge of the conductor turntable 10 forms a cylind...
PUM
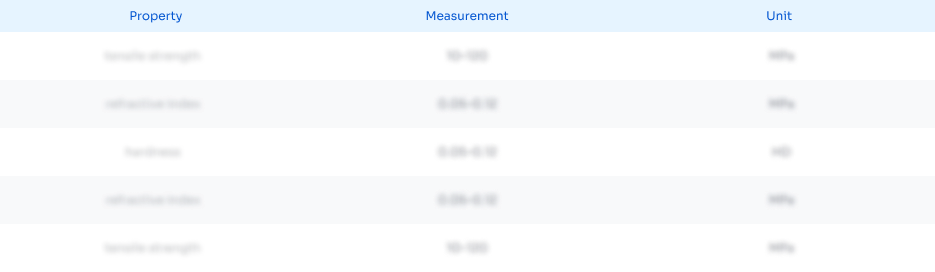
Abstract
Description
Claims
Application Information

- R&D
- Intellectual Property
- Life Sciences
- Materials
- Tech Scout
- Unparalleled Data Quality
- Higher Quality Content
- 60% Fewer Hallucinations
Browse by: Latest US Patents, China's latest patents, Technical Efficacy Thesaurus, Application Domain, Technology Topic, Popular Technical Reports.
© 2025 PatSnap. All rights reserved.Legal|Privacy policy|Modern Slavery Act Transparency Statement|Sitemap|About US| Contact US: help@patsnap.com