Method for constructing and using three-dimensional thermoforming limit diagram of VRB (Variable Thickness Rolled Blanks)
A construction method and technology of forming limit curve, which is applied in the field of construction and application of three-dimensional thermoforming limit diagram of variable thickness plate (VRB), can solve the problems that are not suitable for predicting thermoforming performance of variable thickness plate
- Summary
- Abstract
- Description
- Claims
- Application Information
AI Technical Summary
Problems solved by technology
Method used
Image
Examples
Embodiment Construction
[0044] The following will be combined with the manual Figure 1-14 The present invention is described in detail with embodiment.
[0045] The invention provides a method for constructing a three-dimensional thermoforming limit diagram of a variable-thickness plate, which specifically includes the following steps:
[0046]Step 1. Measure the basic parameters of the sample material at 20°C, wherein the basic parameters of the material include the material thickness anisotropy index r, the material strain hardening index n, and the material constant K;
[0047] The specific calculation refers to the national standard GB / T5028-1999 for the test method of the strain hardening index (n value) of the metal sheet and strip and the national standard GB / T5027-1999 for the test method of the plastic strain ratio (r value) of the metal sheet and strip.
[0048] Such as figure 1 As shown, the sample is made of high-strength boron steel 22MnB5 steel, the thickness is 0.8mm, the gauge leng...
PUM
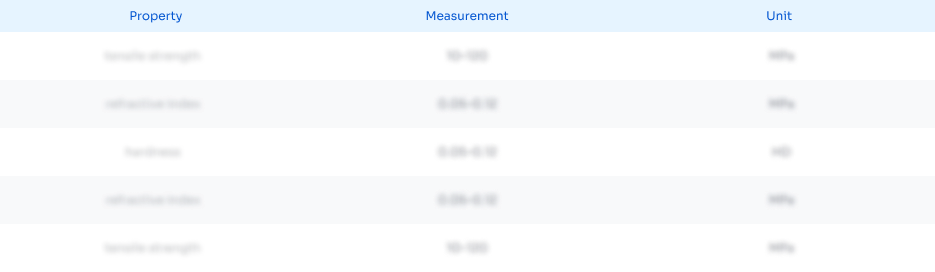
Abstract
Description
Claims
Application Information

- R&D
- Intellectual Property
- Life Sciences
- Materials
- Tech Scout
- Unparalleled Data Quality
- Higher Quality Content
- 60% Fewer Hallucinations
Browse by: Latest US Patents, China's latest patents, Technical Efficacy Thesaurus, Application Domain, Technology Topic, Popular Technical Reports.
© 2025 PatSnap. All rights reserved.Legal|Privacy policy|Modern Slavery Act Transparency Statement|Sitemap|About US| Contact US: help@patsnap.com