Energy Saving and Emission Reduction Method for Carbon Anode Roasting Furnace
An energy-saving and emission-reducing technology for roasting furnaces, applied in furnaces, muffle furnaces, cooking furnaces, etc., can solve problems such as high energy consumption, poor sealing, and insufficient combustion of volatiles, and achieve uniform upper and lower temperatures, reduce energy consumption, The effect of operation process method optimization
- Summary
- Abstract
- Description
- Claims
- Application Information
AI Technical Summary
Problems solved by technology
Method used
Image
Examples
Embodiment Construction
[0026] Such as figure 1 , figure 2 , image 3 with Figure 4 Shown: A method for energy saving and emission reduction of carbon anode baking furnace, the specific methods and measures are as follows:
[0027] 1) Roaster sealing
[0028] 1-1. First, we confirm the length and width of the furnace cover according to the length and width of each furnace chamber of the roasting furnace, and confirm the height of the furnace cover according to the heat dissipation temperature of the furnace surface of the high temperature furnace chamber to obtain the furnace cover length, width and height. size of;
[0029] 1-2. Make a special furnace surface seal furnace cover according to the furnace cover size, use several channel steels 1 to fix the screen 2 on the furnace cover frame 3, and place the flame retardant cloth 4 on the fixing frame 5 at the bottom of the furnace cover frame 3. And fixed by the pressure rod 6 on the side of the furnace cover frame 3, the fiber felt 9 is arranged between...
PUM
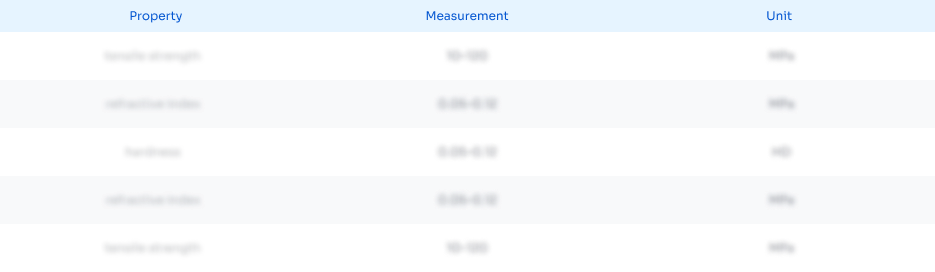
Abstract
Description
Claims
Application Information

- R&D Engineer
- R&D Manager
- IP Professional
- Industry Leading Data Capabilities
- Powerful AI technology
- Patent DNA Extraction
Browse by: Latest US Patents, China's latest patents, Technical Efficacy Thesaurus, Application Domain, Technology Topic, Popular Technical Reports.
© 2024 PatSnap. All rights reserved.Legal|Privacy policy|Modern Slavery Act Transparency Statement|Sitemap|About US| Contact US: help@patsnap.com