Method for preparing alpha-aminoisobutyric acid
A technology of aminoisobutyric acid and ammonia gas, which is applied in the chemical industry to avoid high equipment requirements, solve environmental pollution, and reduce equipment investment
- Summary
- Abstract
- Description
- Claims
- Application Information
AI Technical Summary
Problems solved by technology
Method used
Image
Examples
Embodiment 1
[0037] Add 1800g of water and 587.8g of 98% ammonium carbonate to the 3L reaction kettle, then seal it and preheat it to 60°C, then add 171.9g of 99% acetone cyanohydrin into the reaction kettle with a high-pressure feed pump, and immediately raise the temperature to 160°C , the pressure in the reactor is 5.0MPa, react at this temperature and pressure for 6 hours, then lower the temperature and cool down, then release the pressure and recover carbon dioxide and ammonia through a stripping tower, and the recovered ammonia and carbon dioxide are recycled to prepare ammonium carbonate. The conversion rate of acetone cyanohydrin is 99.9% for the reaction feed liquid obtained by the stripping column. The reaction solution was concentrated, cooled to 0°C for crystallization, and centrifuged to obtain 190.72 g of crude α-aminoisobutyric acid. The yield of α-aminoisobutyric acid was 86% (calculated by acetone cyanohydrin). The content of α-aminoisobutyric acid It is 93% and contains 6...
Embodiment 2
[0040] First add 1800g of water and 483.7g of 98% ammonium bicarbonate to the 3L reactor, then seal it and preheat it to 60°C, then add 171.9g of 99% acetone cyanohydrin into the reactor with a high-pressure feed pump, and immediately raise the temperature to 160 ℃, the pressure in the reactor is 5.0MPa, react at this temperature and pressure for 6 hours, then lower the temperature and cool down, and then release the pressure to recover carbon dioxide and ammonia through the stripping tower, and the recovered ammonia and carbon dioxide are recycled to the preparation of ammonium bicarbonate . The conversion rate of acetone cyanohydrin is 99.9% for the reaction feed liquid obtained by the stripping column. The reaction solution was concentrated, cooled to 0°C for crystallization, and centrifuged to obtain 137.5 g of crude α-aminoisobutyric acid. The yield of α-aminoisobutyric acid was 62% (calculated as acetone cyanohydrin). The content of α-aminoisobutyric acid It is 93% and ...
Embodiment 3
[0043] First add 1800g of water, 587.8g of 98% ammonium carbonate and the crystallization mother liquor obtained in Example 1 into a 3L reactor, then seal and preheat to 60°C, then add 171.9g of 99% acetone into the reactor with a high-pressure feed pump Cyanohydrin, immediately warming up to 160 ℃, the pressure in the reactor is 5.0MPa, react at this temperature and pressure for 6 hours, then cool down and cool down, then release the pressure and pass through the stripping tower to reclaim carbon dioxide and ammonia, the reclaimed ammonia and Carbon dioxide is recycled to make ammonium carbonate. The conversion rate of acetone cyanohydrin is 99.9% for the reaction feed liquid obtained by the stripping column. The reaction solution was concentrated, cooled to 0°C for crystallization, and centrifuged to obtain 199.51 g of crude α-aminoisobutyric acid. The yield of α-aminoisobutyric acid was 89% (calculated by acetone cyanohydrin). The content of α-aminoisobutyric acid It is 92...
PUM
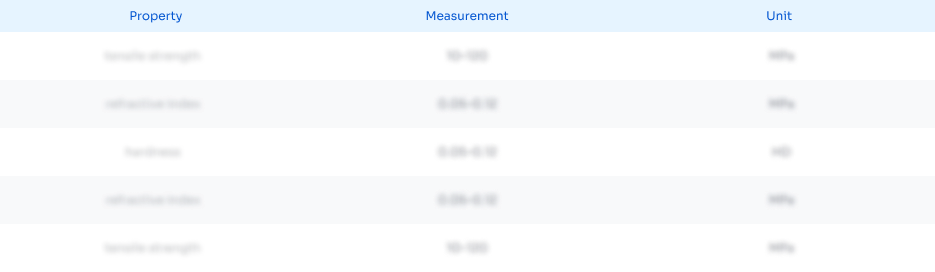
Abstract
Description
Claims
Application Information

- R&D
- Intellectual Property
- Life Sciences
- Materials
- Tech Scout
- Unparalleled Data Quality
- Higher Quality Content
- 60% Fewer Hallucinations
Browse by: Latest US Patents, China's latest patents, Technical Efficacy Thesaurus, Application Domain, Technology Topic, Popular Technical Reports.
© 2025 PatSnap. All rights reserved.Legal|Privacy policy|Modern Slavery Act Transparency Statement|Sitemap|About US| Contact US: help@patsnap.com