Copper powder composition and production method thereof
A composition and technology of copper powder, applied in the field of copper powder production, can solve the problem of not being able to meet the looseness and other problems, and achieve the effects of reducing consumption, uniform particle size and good forming performance
- Summary
- Abstract
- Description
- Claims
- Application Information
AI Technical Summary
Problems solved by technology
Method used
Examples
Embodiment 1
[0035] The preparation method of copper powder composition of the present invention comprises the following steps:
[0036] · The preparation method of electrolytic copper powder, comprises the following steps:
[0037] 1. Copper powder electrolysis: the anode is a cast copper anode plate, and the number of copper anodes is 13; the cathode is a cold-rolled cathode plate, and the number of cathodes is 12; the electrolyte is CuSO4 solution, copper ion: 5g / L; sulfuric acid: 110g / L, chloride ion: 0.5mg / L; electrolytic current density: 1000A / m 2 ; Electrolyte temperature: 45°C.
[0038] Powder scraping: Use a powder scraping machine to brush it up and down twice, and scrape the powder once every 40 minutes.
[0039] 2. Powder washing: use a filter washing machine with a capacity of 3 tons, and wash the powder until it is washed with BaCl 2 Until no white precipitate is detected, the moisture is controlled at 18%.
[0040] 3. Drying and reduction: steel belt furnace is used, an...
Embodiment 2
[0057] The preparation method of copper powder composition of the present invention comprises the following steps:
[0058] · The preparation method of electrolytic copper powder, comprises the following steps:
[0059]1. Copper powder electrolysis: the anode is a cast copper anode plate, and the number of copper anodes is 13; the cathode is a cold-rolled cathode plate, and the number of cathodes is 12; the electrolyte is CuSO4 solution, copper ion: 8g / L; sulfuric acid: 160 g / L, chloride ion: 0.8mg / L; electrolytic current density: 1500A / m 2 ; Electrolyte temperature: 60°C.
[0060] Powder scraping: Use a powder scraping machine to brush it up and down twice, and scrape the powder once every 40 minutes.
[0061] 2. Powder washing: use a filter washing machine with a capacity of 3 tons, and wash the powder until it is washed with BaCl 2 Until no white precipitate is detected, the moisture is controlled at 22%.
[0062] 3. Drying and reduction: steel belt furnace is used, and...
Embodiment 3
[0079] The preparation method of copper powder composition of the present invention comprises the following steps:
[0080] · The preparation method of electrolytic copper powder, comprises the following steps:
[0081] 1. Copper powder electrolysis: the anode is a cast copper anode plate, and the number of copper anodes is 13; the cathode is a cold-rolled cathode plate, and the number of cathodes is 12; the electrolyte is CuSO4 solution, copper ion: 6g / L; sulfuric acid: 130g / L, chloride ion: 0.4mg / L; electrolytic current density: 1300A / m 2 ; Electrolyte temperature: 50°C.
[0082] Powder scraping: Use a powder scraping machine to brush it up and down twice, and scrape the powder once every 40 minutes.
[0083] 2. Powder washing: Use a filter washing machine to wash the powder until it is washed with BaCl 2 Until no white precipitate is detected, the moisture content is controlled at 20%.
[0084] 3. Drying and reduction: steel belt furnace is used, and the conditions are...
PUM
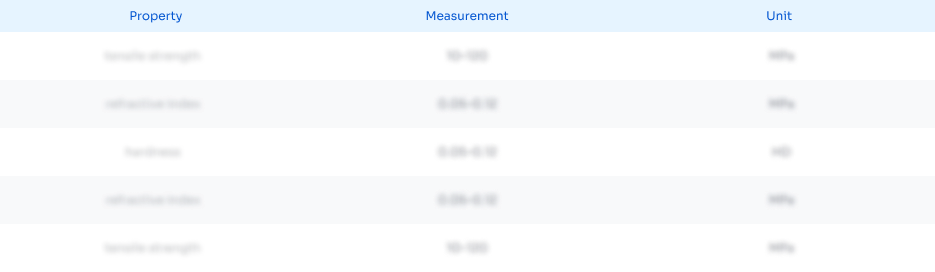
Abstract
Description
Claims
Application Information

- R&D Engineer
- R&D Manager
- IP Professional
- Industry Leading Data Capabilities
- Powerful AI technology
- Patent DNA Extraction
Browse by: Latest US Patents, China's latest patents, Technical Efficacy Thesaurus, Application Domain, Technology Topic, Popular Technical Reports.
© 2024 PatSnap. All rights reserved.Legal|Privacy policy|Modern Slavery Act Transparency Statement|Sitemap|About US| Contact US: help@patsnap.com