Method for improving retention of sizing agent fiber and filler in production of tobacco sheets through paper-making process
A technology of tobacco sheet and paper making method, which is applied in the directions of tobacco, tobacco preparation, application, etc., can solve the problems of loss of pulp fibers and fillers, low utilization rate of raw materials, high waste water treatment volume and high treatment cost, and achieves a reduction in coating rate, The effect is obvious and the effect of improving the utilization rate of raw materials
- Summary
- Abstract
- Description
- Claims
- Application Information
AI Technical Summary
Problems solved by technology
Method used
Image
Examples
Embodiment 1
[0024] Refer to the company's paper-making tobacco sheet production technology and product formula, accurately weigh each tobacco raw material, and implement the separation of chemical components in the tobacco raw material according to the process parameters of the extraction section. The extracted tobacco residue is then passed through a refining process to make tobacco pulp. Add 12% dry weight of tobacco pulp, such as flax fiber and 8% unwrapped filler calcium carbonate, stir thoroughly and adjust to 0.8-1.5% finished pulp. Copy the film on the machine. recorded as a control sample. Determination of fiber and filler retention, substrate ash, bulk and liquid absorption. The measurement results are shown in Table 1.
[0025] Table 1 Determination result 1
[0026]
Embodiment 2
[0044] The present invention is used for papermaking tobacco sheet production to improve the retention method of pulp fiber and filler, and its steps are as follows:
[0045] 1) According to the ratio of 0.01-0.20% by weight, add the natural potato starch of the coating agent and the filler into the reaction kettle, stir well and add deionized water with a total weight of 20-65%, and heat it to a temperature of 45 Stop stirring after -80°C, stop the reaction after the reactants thicken and form a mass, discharge the material, dry in a drying oven at a temperature of 120°C, and grind to 200-600 mesh after completion;
[0046] 2) According to the proportion of the mixed pulp after refining, add a charge regulator to adjust the pulp fiber, and use a particle charge titrator to measure the zeta potential to -25~5mv; the charge regulator is alum. The consumption of described charge modifier is between 0.05-0.25% of the absolute dry weight of slurry;
[0047] 3) After step 2) is co...
PUM
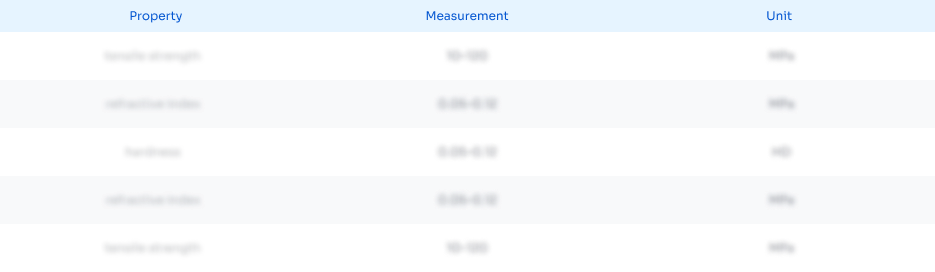
Abstract
Description
Claims
Application Information

- R&D
- Intellectual Property
- Life Sciences
- Materials
- Tech Scout
- Unparalleled Data Quality
- Higher Quality Content
- 60% Fewer Hallucinations
Browse by: Latest US Patents, China's latest patents, Technical Efficacy Thesaurus, Application Domain, Technology Topic, Popular Technical Reports.
© 2025 PatSnap. All rights reserved.Legal|Privacy policy|Modern Slavery Act Transparency Statement|Sitemap|About US| Contact US: help@patsnap.com