Blunt trailing edge wind turbine blade and its trailing edge facade core material fixing method
A fan blade and blunt trailing edge technology, applied in the field of blunt trailing edge fan blades and their trailing edge elevation core material fixation, can solve the problems of trailing edge core material displacement, excessive use of adhesive, etc., to reduce spraying. Adhesive use, the effect of beneficial bonding strength
- Summary
- Abstract
- Description
- Claims
- Application Information
AI Technical Summary
Problems solved by technology
Method used
Image
Examples
Embodiment Construction
[0021] Hereinafter, embodiments of the present invention will be described in detail with reference to the accompanying drawings.
[0022] The method for fixing the core material of the façade of the blunt trailing edge fan blade provided in this embodiment is as follows:
[0023] When laying the façade core material of the blunt trailing edge of the fan blade, at the pre-designed bonding point, cut out a square or other shape gap with the glass fiber cloth of the outer skin, and if there is a release cloth at the place, it also needs to be cut off , forming a through hole. The gap at this time can be the same size for each layer of glass fiber cloth on the outer skin, or it can be cut according to the rule that the gap of the glass fiber cloth close to the core material is small, and the gap of the glass fiber cloth far away from the core material is large. In a word, as long as the through holes are formed on the outer skin at the positions corresponding to the bonding poin...
PUM
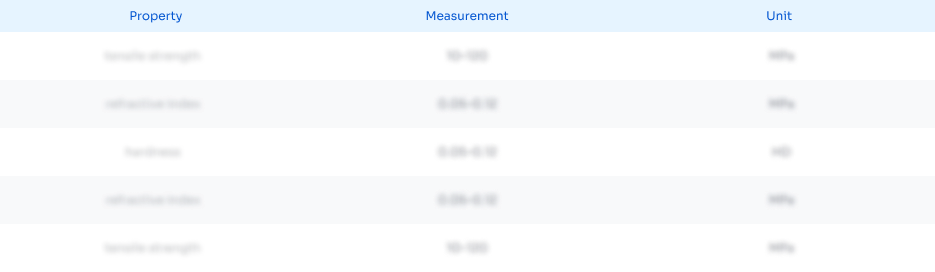
Abstract
Description
Claims
Application Information

- R&D Engineer
- R&D Manager
- IP Professional
- Industry Leading Data Capabilities
- Powerful AI technology
- Patent DNA Extraction
Browse by: Latest US Patents, China's latest patents, Technical Efficacy Thesaurus, Application Domain, Technology Topic, Popular Technical Reports.
© 2024 PatSnap. All rights reserved.Legal|Privacy policy|Modern Slavery Act Transparency Statement|Sitemap|About US| Contact US: help@patsnap.com