Method for controlling pulse combustion of multiple burners of fuel gas furnace
A technology of pulse combustion and gas furnace, which is applied in the field of burner combustion, can solve problems such as failure to meet temperature uniformity requirements, and achieve the effects of good temperature uniformity in the furnace, time and space balance, and energy saving
- Summary
- Abstract
- Description
- Claims
- Application Information
AI Technical Summary
Problems solved by technology
Method used
Image
Examples
Embodiment Construction
[0031] The specific embodiments of the present invention will be further described below in conjunction with the accompanying drawings.
[0032] The invention proposes a new control method aiming at the control of multiple burners in the gas furnace, which does not involve the basic situation of combustion control of a single burner. For each burner to burn normally, the air valve and gas valve are required to provide air and gas respectively, and to ensure a certain reasonable air-fuel ratio, and the burner controller is also required to provide functions such as ignition and flame detection.
[0033] Before the burner works, set the maximum working cycle time Tonmax and the minimum working cycle time Tonmin of the burner combustion.
[0034] Such as figure 1 As shown, after the controller receives the actual temperature measured by the temperature sensor, it compares it with the set temperature to obtain a temperature difference signal, performs PID calculation, and outputs...
PUM
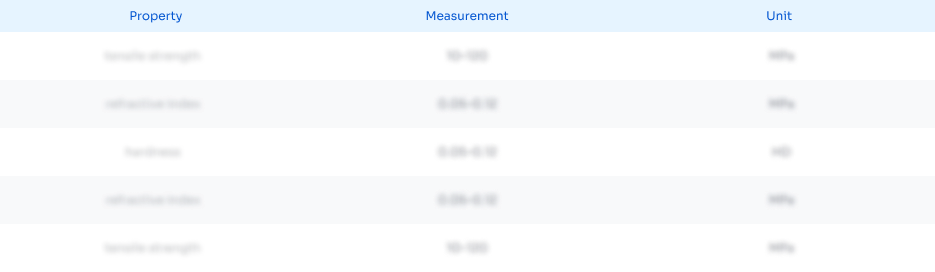
Abstract
Description
Claims
Application Information

- Generate Ideas
- Intellectual Property
- Life Sciences
- Materials
- Tech Scout
- Unparalleled Data Quality
- Higher Quality Content
- 60% Fewer Hallucinations
Browse by: Latest US Patents, China's latest patents, Technical Efficacy Thesaurus, Application Domain, Technology Topic, Popular Technical Reports.
© 2025 PatSnap. All rights reserved.Legal|Privacy policy|Modern Slavery Act Transparency Statement|Sitemap|About US| Contact US: help@patsnap.com