A method for forming a hollow composite material pipe body
A composite material and molding method technology, which is applied in the field of composite material manufacturing, can solve the problems of strong friction between the pipe body and the core mold, insufficient extrusion amount, and poor product glue, so as to reduce the input cost, improve the success rate, and reduce the production cycle. the effect of shortening
- Summary
- Abstract
- Description
- Claims
- Application Information
AI Technical Summary
Problems solved by technology
Method used
Image
Examples
Embodiment 1
[0028] right figure 1 The hollow square tube shown is produced, and the forming steps are as follows:
[0029] 1.1 Use metal aluminum plate or stainless steel sheet to preform according to the inner profile of the square tube, and manufacture a half-profile "L"-shaped metal partition with a thickness of 0.5mm;
[0030] 1.2 Manufacture the metal mandrel and composite material shape tooling that removes the thickness of the partition: the thickness of 0.5mm must be subtracted when the metal mandrel is manufactured, and the surface formed by the metal mandrel plus the metal partition conforms to the theoretical internal shape of the product, and the composite material The shape tooling is the upper and lower clamping structure, and the profile of the clamping structure is the external profile of the product;
[0031] 1.3 Cover two "L"-shaped metal partitions on the metal mandrel, and connect the metal partitions with adhesive tape to form a whole;
[0032] 1.4 Lay layers on met...
Embodiment 2
[0038] right figure 2 The hollow circular tube shown is produced, and the forming steps are as follows:
[0039] 2.1 Use metal aluminum plate or stainless steel sheet to preform according to the inner surface of the round tube, and manufacture a metal partition with a thickness of 0.5mm and a semicircular surface;
[0040] 2.2 Manufacture the metal mandrel and composite material shape tooling that removes the thickness of the partition: the thickness of 0.5mm must be subtracted when the metal mandrel is manufactured, and the surface formed by the metal mandrel plus the metal partition conforms to the theoretical internal shape of the product, and the composite The shape tooling is the upper and lower clamping structure, and the profile of the clamping structure is the external profile of the product;
[0041] 2.3 Cover two semicircular metal partitions on the metal mandrel, and connect the metal partitions with adhesive tape to form a whole;
[0042] 2.4 Lay layers on the p...
PUM
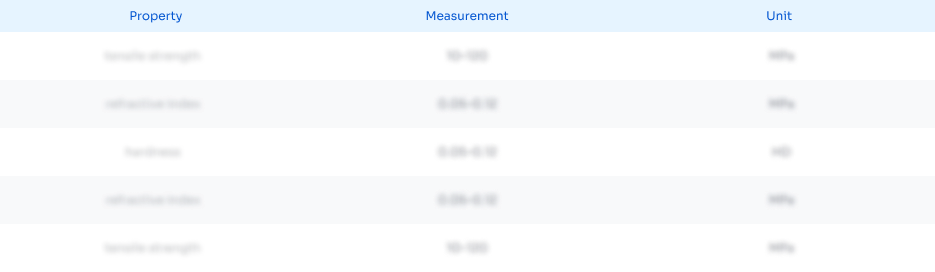
Abstract
Description
Claims
Application Information

- R&D Engineer
- R&D Manager
- IP Professional
- Industry Leading Data Capabilities
- Powerful AI technology
- Patent DNA Extraction
Browse by: Latest US Patents, China's latest patents, Technical Efficacy Thesaurus, Application Domain, Technology Topic, Popular Technical Reports.
© 2024 PatSnap. All rights reserved.Legal|Privacy policy|Modern Slavery Act Transparency Statement|Sitemap|About US| Contact US: help@patsnap.com