Reducing blow molding packing barrel and preparation method thereof
A packaging barrel and weight reduction technology, which is applied in the field of blow molding plastics, can solve the problems of cost reduction and achieve the effects of reduced material consumption, high output power, and uniform wall thickness
- Summary
- Abstract
- Description
- Claims
- Application Information
AI Technical Summary
Problems solved by technology
Method used
Examples
Embodiment 1
[0028] The invention provides a reduced-weight blow-molded packaging barrel and a preparation method thereof, comprising the following process steps:
[0029] (1) Weigh 100 parts of high-density polyethylene and place it in a mixer, first add 1.5 parts of epoxy linseed oil, 0.1 part of 2-hydroxy-4-n-octyloxybenzophenone, and 1 part of stearin Calcium acid, 2 parts of nitrile powder rubber, adjust the speed of the mixer to 5m / s, the temperature is 30 ℃, mix and stir for 10 minutes, then add 0.09 parts of antioxidant 1010 and 0.08 parts of dilauryl thiodipropionate , adjust the speed of the mixer to 4m / s, the temperature to 70°C, mix and stir for 10 minutes, and mix into a mixture;
[0030] (2) Put the mixture in the hopper of the conical twin-screw extruder. The barrel is a seven-section barrel structure, the seventh section of the barrel is the die head, and the temperature of the barrel is set to: 120°C in the first zone and 128 in the second zone. ℃, 130℃ in the third zone,...
Embodiment 2
[0036] The invention provides a reduced-weight blow-molded packaging barrel and a preparation method thereof, comprising the following process steps:
[0037] (1) Weigh 100 parts of high-density polyethylene and place it in a mixer, first add 2.5 parts of epoxy linseed oil, 0.3 parts of 2-hydroxy-4-n-octyloxybenzophenone, and 0.5 parts of stearin Calcium acid, 0.5 parts of nitrile powder rubber, adjust the speed of the mixer to 6m / s, the temperature is 45 ° C, mix and stir for 10 minutes, then add 0.06 parts of antioxidant 1010 and 0.1 part of dilauryl thiodipropionate , adjust the speed of the mixer to 5m / s, the temperature to 50°C, mix and stir for 10 minutes, and mix into a mixture;
[0038] (2) Put the mixture in the hopper of the conical twin-screw extruder. The barrel is a seven-section barrel structure, the seventh section of the barrel is the die head, and the temperature of the barrel is set to: 125°C in the first zone and 135 in the second zone. ℃, the third zone is...
Embodiment 3
[0044] The invention provides a reduced-weight blow-molded packaging barrel and a preparation method thereof, comprising the following process steps:
[0045] (1) Weigh 100 parts of high-density polyethylene and place it in a mixer, first add 2 parts of epoxy linseed oil, 0.2 parts of 2-hydroxy-4-n-octyloxybenzophenone, and 0.8 parts of stearin Calcium acid, 1 part of nitrile powder rubber, adjust the speed of the mixer to 5m / s, the temperature is 40 ° C, mix and stir for 10 minutes, then add 0.08 parts of antioxidant 1010 and 0.09 parts of dilauryl thiodipropionate , adjust the speed of the mixer to 5m / s, the temperature to 60°C, mix and stir for 10 minutes, and mix into a mixture;
[0046] (2) Put the mixture in the hopper of the conical twin-screw extruder. The barrel is a seven-section barrel structure, the seventh section of the barrel is the die head, and the temperature of the barrel is set to: 123°C in the first zone and 130 in the second zone. ℃, the third zone is 13...
PUM
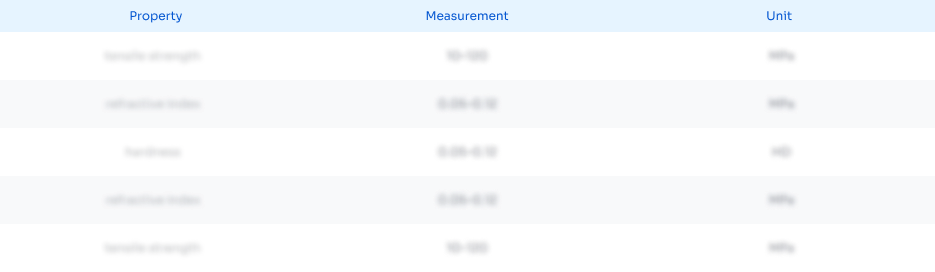
Abstract
Description
Claims
Application Information

- R&D Engineer
- R&D Manager
- IP Professional
- Industry Leading Data Capabilities
- Powerful AI technology
- Patent DNA Extraction
Browse by: Latest US Patents, China's latest patents, Technical Efficacy Thesaurus, Application Domain, Technology Topic, Popular Technical Reports.
© 2024 PatSnap. All rights reserved.Legal|Privacy policy|Modern Slavery Act Transparency Statement|Sitemap|About US| Contact US: help@patsnap.com