T-shaped guide rail automatic machining process
An automatic processing and guide rail technology, applied in the direction of linear motion bearings, bearings, shafts and bearings, can solve problems affecting production cycle time, manual finishing, product processing surface collisions, bruises, etc., to eliminate surface paint peeling The effect of rusting, improving the workshop environment, and increasing the rigidity of equipment
- Summary
- Abstract
- Description
- Claims
- Application Information
AI Technical Summary
Problems solved by technology
Method used
Image
Examples
Embodiment Construction
[0033] In order to make the object, technical solution and advantages of the present invention clearer, the present invention will be further described in detail below in conjunction with the accompanying drawings and embodiments. It should be understood that the specific embodiments described here are only used to explain the present invention, not to limit the present invention.
[0034] T-shaped guide rail automatic processing technology of the present invention is as figure 1 As shown, the specific steps of the processing technology are as follows:
[0035] (1) rust removal
[0036] The steel shot particles are sprayed onto the surface of the guide rail to remove the scale on the surface of the guide rail, and the iron dust is collected with a dust bag and an environmental protection dust removal device.
[0037] Compared with the traditional wire wheel dust removal, this improves the environment, reduces labor intensity, reduces labor capacity costs (originally changed ...
PUM
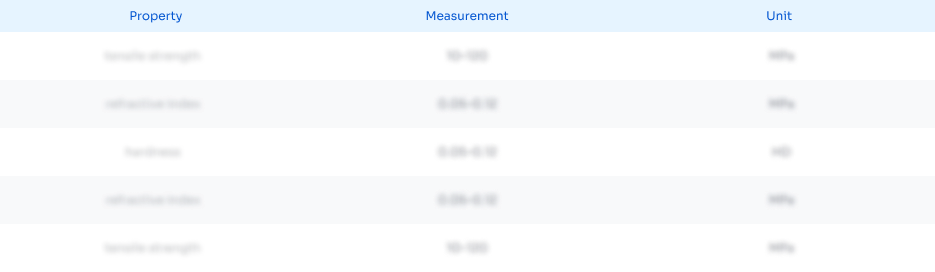
Abstract
Description
Claims
Application Information

- R&D Engineer
- R&D Manager
- IP Professional
- Industry Leading Data Capabilities
- Powerful AI technology
- Patent DNA Extraction
Browse by: Latest US Patents, China's latest patents, Technical Efficacy Thesaurus, Application Domain, Technology Topic, Popular Technical Reports.
© 2024 PatSnap. All rights reserved.Legal|Privacy policy|Modern Slavery Act Transparency Statement|Sitemap|About US| Contact US: help@patsnap.com