Oil storing bearing mechanism
A bearing and oil storage technology, which is applied in the fields of plastics, textiles, printing and dyeing equipment, papermaking, and tanning, and can solve problems such as lubrication without oil storage, disturbance constant tension, and fabric tension fluctuations
- Summary
- Abstract
- Description
- Claims
- Application Information
AI Technical Summary
Problems solved by technology
Method used
Image
Examples
Embodiment Construction
[0013] Such as figure 1 As shown, the present invention includes a bearing seat 1, and a double-row self-aligning bearing 2 is arranged in the center of the inner hole of the bearing seat 1, and the double-row self-aligning bearing 2 is sleeved on the outside of the guide roller journal 3; in the double-row self-aligning bearing 2. The journal grinding discs 4 are respectively set on the guide roller journals 3 on both sides, and a fluorine rubber "O" sealing ring 5 is respectively set between each journal grinding disc 4 and the guide roller journal 3; Fluorine rubber grooved oil seals 6 are respectively set in the inner hole of the seat 1 and both sides of the double-row self-aligning bearing 2; screw holes 7 are respectively set on the two end faces of the bearing seat 1, and magnetic screws are threaded in each screw hole 7 8. Each fluorine rubber grooved oil seal 6 is locked with the double-row self-aligning bearing 2 and the bearing seat 1 through the magnetic screw 8 re...
PUM
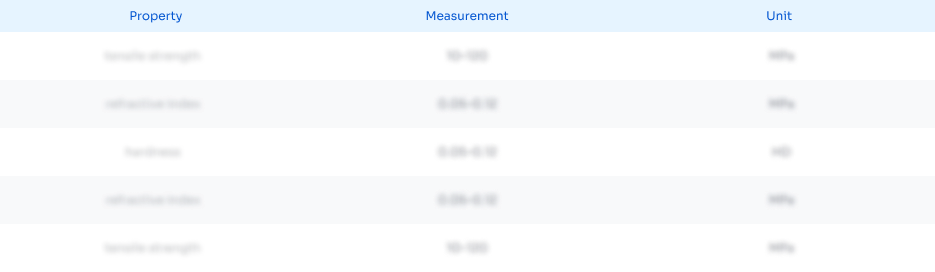
Abstract
Description
Claims
Application Information

- Generate Ideas
- Intellectual Property
- Life Sciences
- Materials
- Tech Scout
- Unparalleled Data Quality
- Higher Quality Content
- 60% Fewer Hallucinations
Browse by: Latest US Patents, China's latest patents, Technical Efficacy Thesaurus, Application Domain, Technology Topic, Popular Technical Reports.
© 2025 PatSnap. All rights reserved.Legal|Privacy policy|Modern Slavery Act Transparency Statement|Sitemap|About US| Contact US: help@patsnap.com