A busbar conductive connection terminal
A technology for connecting terminals and busbars, applied in the direction of contact parts, etc., can solve the problems of excessive temperature rise at the terminals, easy to loose, poor contact, etc., to reduce the risk of expansion and looseness, increase the contact area, and enhance the conductivity. Effect
- Summary
- Abstract
- Description
- Claims
- Application Information
AI Technical Summary
Problems solved by technology
Method used
Image
Examples
Embodiment Construction
[0026] like figure 2 and image 3 As shown, the copper pad in an embodiment of the present invention is formed by vertically connecting two cylinders, and the diameter of the upper cylinder is smaller than the diameter of the lower cylinder; the connection between the upper cylinder and the lower cylinder is provided with a groove 4 The bottom end of the groove 4 is connected to the upper bottom surface of the lower cylinder through the boss 5, and the boss 5 includes a horizontal part connected to the bottom end of the groove 4, and the horizontal part is connected to the bottom of the groove through an inclined part. The upper bottom surface of the lower cylinder is connected, and the angle between the horizontal part and the inclined part is greater than or equal to 90°.
[0027] like Figure 8 As shown, the middle part of the copper plate of the present invention is provided with an installation hole 7 whose size matches the outer diameter of the above-mentioned upper c...
PUM
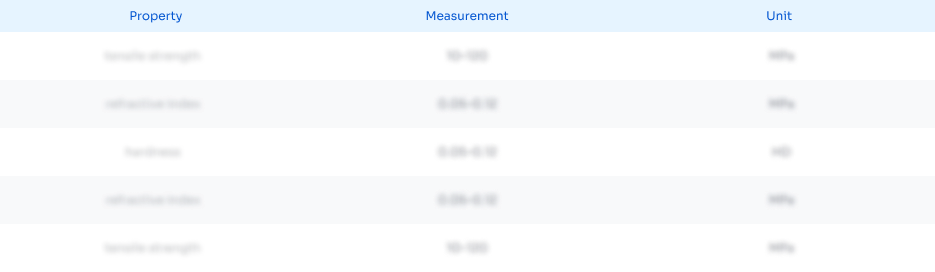
Abstract
Description
Claims
Application Information

- R&D Engineer
- R&D Manager
- IP Professional
- Industry Leading Data Capabilities
- Powerful AI technology
- Patent DNA Extraction
Browse by: Latest US Patents, China's latest patents, Technical Efficacy Thesaurus, Application Domain, Technology Topic, Popular Technical Reports.
© 2024 PatSnap. All rights reserved.Legal|Privacy policy|Modern Slavery Act Transparency Statement|Sitemap|About US| Contact US: help@patsnap.com