Scalable underactuated cable-strut truss gripper
A manipulator and truss-type technology, applied in the field of modular manipulators, can solve the problems of poor adaptability to the shape of the target object, difficult expansion of the SARAH gripper, heavy weight of the SARAH gripper, etc., and achieves strong target adaptability and mature processing technology. , the effect of rich material resources
- Summary
- Abstract
- Description
- Claims
- Application Information
AI Technical Summary
Problems solved by technology
Method used
Image
Examples
specific Embodiment approach 1
[0019] Specific implementation mode one: combine Figure 1-Figure 4 Explain that an expandable underactuated cable-strut truss gripper in this embodiment includes a front-end connection device, an inter-rod rotation angle limiting mechanism 9, an end cable-strut truss 12, ropes, multiple positioning columns 10 and multiple expandable modules Cable-strut truss 6;
[0020] The front connecting device comprises a connecting plate 1, two rope shafts 2, two spacer posts 5, two mounting plates 4, two transition plates 18 and four supporting plates 3, and one end surface of the connecting plate 1 is equipped with four A support plate 3, four support plates 3 are arranged in a rectangular array, two support plates 3 on the same side in the vertical direction are provided with rope shafts 2, and two mounting plates 4 are installed on the upper surface of the connecting plate 1, Each mounting plate 4 is fixed with a motor 17, the output shaft of the motor 17 is vertically arranged and ...
specific Embodiment approach 2
[0029] Specific implementation mode two: combination figure 1 To illustrate, the frictional damping metal sheet 8 in this embodiment is a steel sheet. Such a setting is cheap and easy to obtain, and changing the pressure at both ends of the frictional damping can change the resistance torque between the two rods, thereby realizing the controllable design of the underactuated mechanism. Others are the same as in the first embodiment.
specific Embodiment approach 3
[0030] Specific implementation mode three: combination figure 1 To illustrate, the frictional damping metal sheet 8 in this embodiment is an aluminum sheet. Such a setting is cheap and easy to obtain, and changing the pressure at both ends of the frictional damping can change the resistance torque between the two rods, thereby realizing the controllable design of the underactuated mechanism. Others are the same as in the first embodiment.
PUM
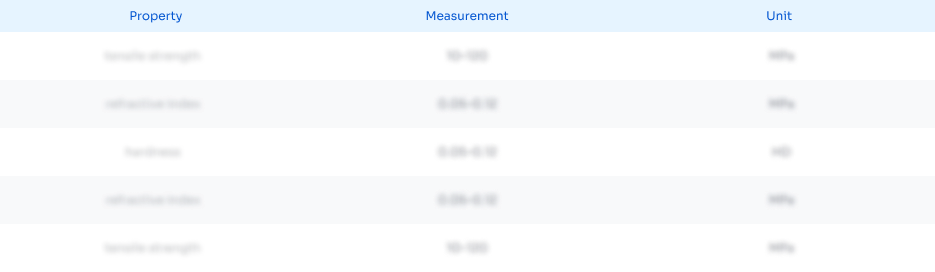
Abstract
Description
Claims
Application Information

- R&D
- Intellectual Property
- Life Sciences
- Materials
- Tech Scout
- Unparalleled Data Quality
- Higher Quality Content
- 60% Fewer Hallucinations
Browse by: Latest US Patents, China's latest patents, Technical Efficacy Thesaurus, Application Domain, Technology Topic, Popular Technical Reports.
© 2025 PatSnap. All rights reserved.Legal|Privacy policy|Modern Slavery Act Transparency Statement|Sitemap|About US| Contact US: help@patsnap.com