Parallel micromanipulation robot
A micro-manipulation and robot technology, applied in manipulators, program-controlled manipulators, manufacturing tools, etc., can solve the problems of less freedom of operation, low motion resolution, and small operating range, so as to improve operating performance, high motion resolution, The effect of a large operating range
- Summary
- Abstract
- Description
- Claims
- Application Information
AI Technical Summary
Problems solved by technology
Method used
Image
Examples
Embodiment Construction
[0019] like figure 1 and figure 2 The parallel micro-manipulation robot shown includes a left micro-manipulator 1 and a right micro-manipulator 2 with the same structure and arranged symmetrically. The left micromanipulator includes a semi-cylindrical left micromanipulator mobile phone holder 8, the first branch chain 6, the second branch chain 7, the third branch chain 9, the left micromanipulator manual platform 18 and the left micromanipulator hand end tool 5. The right micromanipulator includes a semi-cylindrical right micromanipulator mobile phone holder 12, the fourth branch chain 10, the fifth branch chain 11, the sixth branch chain 13, the right micromanipulator manual platform and the right micromanipulator end tool 3.
[0020] image 3 In the left micro-manipulator shown, each branch chain includes a micro-displacement driver 15, a flexible moving pair 14 and two branches with the same structure, and each branch is composed of two flexible ball joints 16 and a ri...
PUM
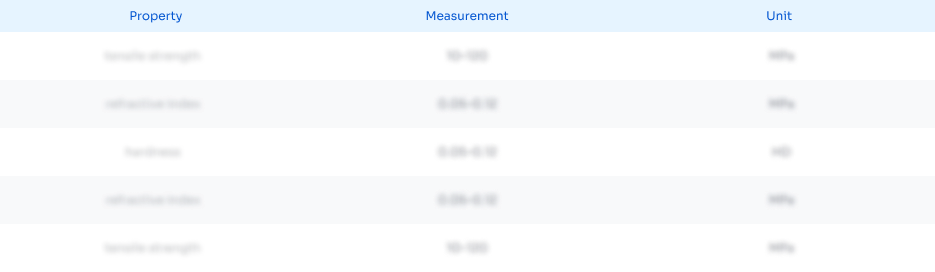
Abstract
Description
Claims
Application Information

- R&D
- Intellectual Property
- Life Sciences
- Materials
- Tech Scout
- Unparalleled Data Quality
- Higher Quality Content
- 60% Fewer Hallucinations
Browse by: Latest US Patents, China's latest patents, Technical Efficacy Thesaurus, Application Domain, Technology Topic, Popular Technical Reports.
© 2025 PatSnap. All rights reserved.Legal|Privacy policy|Modern Slavery Act Transparency Statement|Sitemap|About US| Contact US: help@patsnap.com