Method for manufacturing multi-section cylindrical cast coil wound with round winding wire
A technology of casting coils and manufacturing methods, which is applied in the field of transformer manufacturing, can solve problems such as easy-to-damage coil insulation, difficult positioning of sets, and inconvenient operation, and achieve the effects of high electric strength, high electric strength, energy saving, and convenient operation
- Summary
- Abstract
- Description
- Claims
- Application Information
AI Technical Summary
Problems solved by technology
Method used
Image
Examples
Embodiment 1
[0037] Example 1: 10KV, D-connection segmented cylindrical casting coil
[0038] A multi-segment cylindrical casting coil wound with 10KV round winding wire, divided into 8 segments, each segment voltage is about 10000X1. Connect the middle section M led by the tap, wind it rightward and reversely, and wind it according to the circular winding wire 1 to form an isosceles trapezoidal arrangement in cross section. In the second step, place the special-shaped positioning block 2, and then continue to wind the section N. According to the circular winding wire 1, the cross-section is arranged as a parallelogram, and the third step is to place the special-shaped positioning block 2, and then continue to wind the segment O, according to the circular winding wire 1, the cross-section is arranged as a parallelogram, and the fourth step is to place After the special-shaped positioning block 2, continue to wind the segment P at last, wind the round winding wire 1 into a parallelogram in ...
Embodiment 2
[0039] Example 2: 20KV, D-connection segmented cylindrical casting coil
[0040]A multi-segment cylindrical casting coil made of 20KV round winding wire, divided into 12 segments, first winding 6 segments on the left half-phase, and then winding 6 segments on the right half-phase, the voltage of each segment is about 20000X1.05 / 12=1750V, the first The winding method from the first step to the fourth step is the same as the multi-section cylindrical casting coil wound by the 10KV round winding wire, the difference is that after the third step, two round winding wires are added to form a parallelogram arrangement in cross section. segment.
Embodiment 3
[0041] Example 3: 35KV, D-connection segmented cylindrical casting coil
[0042] A multi-segment cylindrical casting coil made of 35KV round winding wire, divided into 22 segments, the voltage of each segment is about 35000X1.05 / 22=1670.5V. The winding method from the first step to the fourth step is the same as that of the 10KV multi-segment cylindrical casting coil wound with a round winding wire. The difference is that after the third step, nine coils are wound according to the round winding wire 1 to form a parallelogram arrangement in cross section. segment.
[0043] The multi-section cylindrical casting coil wound by 35KV round winding wire can also be divided into any integer section within 12 to 22. At this time, the voltage of each section and each layer will increase accordingly, and the interlayer insulation must be thickened. distance. How many sections are used must be optimized according to other technical performance indicators (such as: impedance voltage) and...
PUM
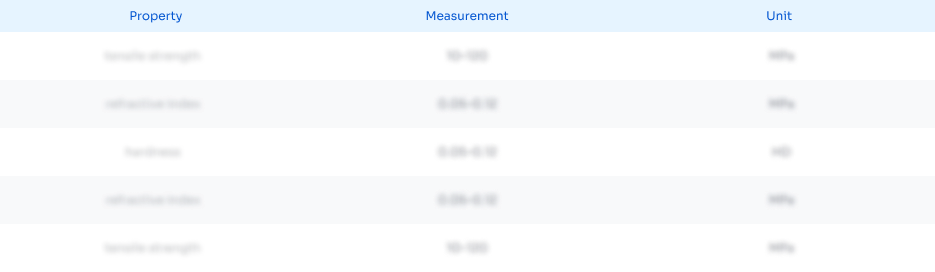
Abstract
Description
Claims
Application Information

- R&D Engineer
- R&D Manager
- IP Professional
- Industry Leading Data Capabilities
- Powerful AI technology
- Patent DNA Extraction
Browse by: Latest US Patents, China's latest patents, Technical Efficacy Thesaurus, Application Domain, Technology Topic, Popular Technical Reports.
© 2024 PatSnap. All rights reserved.Legal|Privacy policy|Modern Slavery Act Transparency Statement|Sitemap|About US| Contact US: help@patsnap.com