Micromechanical structure
A micro-mechanical structure and micro-mechanical technology, applied in micro-structure technology, micro-structure devices, micro-structure devices composed of deformable elements, etc., can solve problems such as deterioration of sensor resolution, and achieve cost minimization and small dependence. The effect of low sex and space requirements
- Summary
- Abstract
- Description
- Claims
- Application Information
AI Technical Summary
Problems solved by technology
Method used
Image
Examples
Embodiment Construction
[0016] Identical parts are always provided with the same reference numerals in different figures and are therefore usually also named or mentioned only once in each case.
[0017] exist figure 1 A schematic schematic diagram of a micromechanical structure according to the invention, in particular a rotational speed sensor, is shown in . The micromechanical structure is denoted overall with the reference number 1 . The micromechanical structure 1 has a substrate, which is shown only schematically and is designated by reference numeral 110 . The substrate 110 has a main extension plane 100, which in figure 1 is illustrated schematically at the bottom right with the second direction 102 and the third direction 103 and the axis designation x for the second direction 102 and the axis designation y for the third direction 103 . The first direction 101 can be considered to extend perpendicularly to the main extension plane 100 and is also given the designation z. The micromechani...
PUM
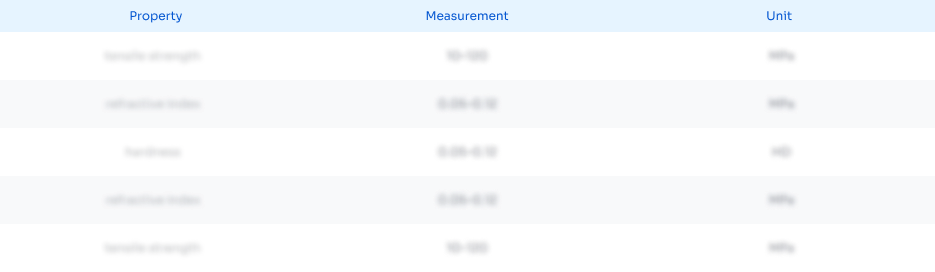
Abstract
Description
Claims
Application Information

- R&D
- Intellectual Property
- Life Sciences
- Materials
- Tech Scout
- Unparalleled Data Quality
- Higher Quality Content
- 60% Fewer Hallucinations
Browse by: Latest US Patents, China's latest patents, Technical Efficacy Thesaurus, Application Domain, Technology Topic, Popular Technical Reports.
© 2025 PatSnap. All rights reserved.Legal|Privacy policy|Modern Slavery Act Transparency Statement|Sitemap|About US| Contact US: help@patsnap.com