Wood veneer advanced compound material manufacturing method
A manufacturing method and technology of wood veneer, which are used in the joining of wood veneers, manufacturing tools, wood processing appliances, etc., can solve the problem of low strength of wood veneer composite materials, low utilization rate of wood resources, and failure to reach engineering materials. requirements and other issues, to achieve significant economic and social benefits, high utilization of wood resources, and easy operation.
- Summary
- Abstract
- Description
- Claims
- Application Information
AI Technical Summary
Problems solved by technology
Method used
Image
Examples
Embodiment 1
[0012] A method for manufacturing advanced wood veneer composite materials, comprising the following steps: (1) according to the volume ratio V 酚醛树脂胶黏剂 :V 环氧树脂胶黏剂 :V 聚胺酯胶黏剂 =1:0.2:0.35, uniformly mix phenolic resin adhesive, epoxy resin adhesive and polyurethane adhesive to obtain composite adhesive, wherein the solid content of phenolic resin adhesive is 60%, epoxy resin adhesive The solid content of the resin adhesive is 50%, and the solid content of the polyurethane adhesive is 40%; (2) Spray the composite adhesive on the surface of the wood veneer, glass fiber mesh and copper mesh, and the spraying amount is 200g / m 2 , where the thickness of wood veneer is 1.0mm, and the diameter of glass fiber and copper wire is 0.08mm; (3) According to figure 1 Carry out slab assembly, the thickness of the slab is 60mm, and then hot press at 100°C and a pressure of 1.5MPa for 5min to make the moisture content 12%.
Embodiment 2
[0014] A method for manufacturing advanced wood veneer composite materials, comprising the following steps: (1) according to the volume ratio V 酚醛树脂胶黏剂 :V 环氧树脂胶黏剂 :V 聚胺酯胶黏剂 =1:0.3:0.35, uniformly mix phenolic resin adhesive, epoxy resin adhesive and polyurethane adhesive to obtain composite adhesive, wherein the solid content of phenolic resin adhesive is 40%, epoxy resin adhesive The solid content of the resin adhesive is 45%, and the solid content of the polyurethane adhesive is 60%; (2) Spray the composite adhesive on the surface of the wood veneer, glass fiber mesh and copper mesh, and the spraying amount is 220g / m 2 , in which the thickness of wood veneer is 1.2mm, and the diameter of glass fiber and copper wire is 0.09mm; (3) According to figure 1 Carry out slab assembly, the slab thickness is 80mm, and then hot press at 120°C and 3.5MPa pressure for 10min to make the moisture content 8%.
Embodiment 3
[0016] A method for manufacturing advanced wood veneer composite materials, comprising the following steps: (1) according to the volume ratio V 酚醛树脂胶黏剂 :V 环氧树脂胶黏剂 :V 聚胺酯胶黏剂 =1:0.2:0.25, uniformly mix the phenolic resin adhesive, epoxy resin adhesive and polyurethane adhesive to obtain a composite adhesive, in which the phenolic resin adhesive, epoxy resin adhesive and polyurethane The solid content of the adhesive is 60% respectively; (2) The composite adhesive is sprayed on the surface of wood veneer, glass fiber mesh and copper mesh, and the spraying amount is 180g / m 2 , in which the thickness of wood veneer is 0.6mm, and the diameter of glass fiber and copper wire is 0.07mm; (3) according to figure 1 Carry out slab assembly, the thickness of the slab is 70mm, and then hot press at 100°C and a pressure of 2.5MPa for 20min to make the moisture content 9%.
PUM
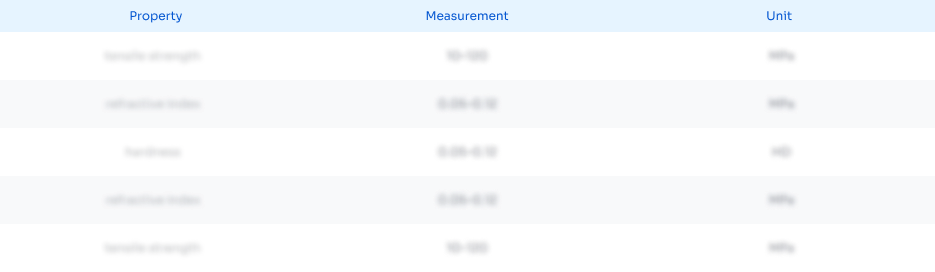
Abstract
Description
Claims
Application Information

- R&D Engineer
- R&D Manager
- IP Professional
- Industry Leading Data Capabilities
- Powerful AI technology
- Patent DNA Extraction
Browse by: Latest US Patents, China's latest patents, Technical Efficacy Thesaurus, Application Domain, Technology Topic, Popular Technical Reports.
© 2024 PatSnap. All rights reserved.Legal|Privacy policy|Modern Slavery Act Transparency Statement|Sitemap|About US| Contact US: help@patsnap.com