Dynamic process fault forecasting method based on fuzzy self-adaptive prediction
A fuzzy self-adaptive, dynamic process technology, applied in special data processing applications, instruments, electrical digital data processing, etc., can solve problems such as the difficulty of determining the normal operating range and the fact that state variables have no actual physical meaning.
- Summary
- Abstract
- Description
- Claims
- Application Information
AI Technical Summary
Problems solved by technology
Method used
Image
Examples
Embodiment
[0075] In this example, the dynamic process fault prediction method is applied to the non-adiabatic continuous stirred reactor (CSTR) process. The non-adiabatic continuous stirred reactor is a typical chemical production unit. thermal response A r →B r , the heat is taken away through the cooling jacket, and the specific model is described as follows:
[0076] dC A dt = - k 0 e - E RT C A + F ( C F - C A ) V
[0077] dT dt = ...
PUM
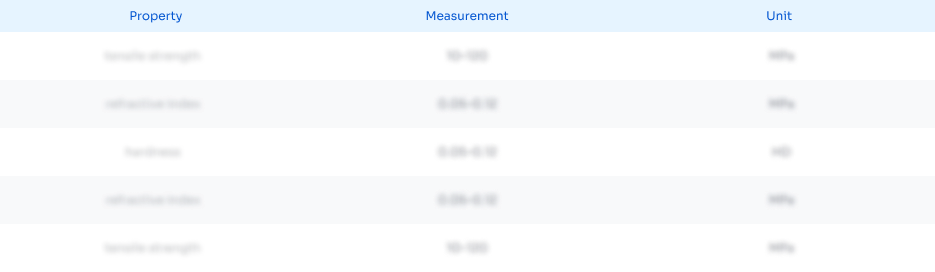
Abstract
Description
Claims
Application Information

- R&D Engineer
- R&D Manager
- IP Professional
- Industry Leading Data Capabilities
- Powerful AI technology
- Patent DNA Extraction
Browse by: Latest US Patents, China's latest patents, Technical Efficacy Thesaurus, Application Domain, Technology Topic, Popular Technical Reports.
© 2024 PatSnap. All rights reserved.Legal|Privacy policy|Modern Slavery Act Transparency Statement|Sitemap|About US| Contact US: help@patsnap.com