While-drilling reflecting sound wave measuring sound system
An acoustic measurement, while drilling technology, applied in measurement, earth-moving drilling, wellbore/well components, etc., can solve the problems of inability to obtain the drilling trajectory of the wellbore, low resolution, and difficulty in specific locations, and achieve easy data processing. Interpretation, reduction of interfering signals, the effect of simple device structure
- Summary
- Abstract
- Description
- Claims
- Application Information
AI Technical Summary
Problems solved by technology
Method used
Image
Examples
Embodiment Construction
[0025] Such as figure 1 As shown, the sound system for measuring reflected acoustic waves while drilling includes: a drill collar 100, an acoustic wave emitting transducer 101 is arranged outside the middle of the drill collar 100, and the acoustic wave emitting transducer 101 is a single acoustic wave transducer;
[0026] The first close-source acoustic wave receiving transducer 102 and the second close-source acoustic wave receiving transducer 102' are arranged symmetrically with respect to the acoustic wave transmitting transducer 101 in the axial direction of the drill collar 100, and the first close-source acoustic wave receiving transducer Both the device 102 and the second close-source acoustic wave receiving transducer 102' are single acoustic wave transducers;
[0027] The first far-source distance acoustic wave receiving transducer array 103 and the second far-source distance acoustic wave receiving transducer array 103' are arranged symmetrically with respec...
PUM
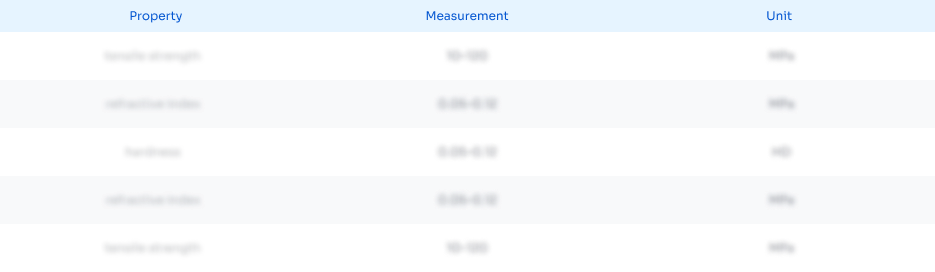
Abstract
Description
Claims
Application Information

- R&D
- Intellectual Property
- Life Sciences
- Materials
- Tech Scout
- Unparalleled Data Quality
- Higher Quality Content
- 60% Fewer Hallucinations
Browse by: Latest US Patents, China's latest patents, Technical Efficacy Thesaurus, Application Domain, Technology Topic, Popular Technical Reports.
© 2025 PatSnap. All rights reserved.Legal|Privacy policy|Modern Slavery Act Transparency Statement|Sitemap|About US| Contact US: help@patsnap.com