Yarn unwinding system
An unwinding and yarn technology, applied in textiles and papermaking, weft knitting, knitting and other directions, can solve the problems of large variation in unwinding resistance, uneven tension, complex structure, etc. Consistent effect around conditions
- Summary
- Abstract
- Description
- Claims
- Application Information
AI Technical Summary
Problems solved by technology
Method used
Image
Examples
Embodiment Construction
[0019] The outer creel of the traditional circular weft machine is horizontal unwinding. When the traditional circular weft machine is used to unwind the metal fiber yarn, there will be the following problems: when the yarn is unwound along the horizontal direction, it will rotate around the bobbin to form Balloon, the influence of the weight of the yarn on the shape of the balloon is far greater than that of conventional textile yarns, causing friction between the yarn and the surface of the bobbin, and the friction between the yarn and the surface of the bobbin when the yarn is on the centerline of the shaft and down The length and unwinding conditions are inconsistent, resulting in uneven tension and large changes in unwinding resistance.
[0020] In view of the above-mentioned problems existing in the prior art, it is necessary to design a yarn unwinding system specially suitable for pure metal yarn unwinding conditions.
[0021] The invention discloses a yarn unwinding sy...
PUM
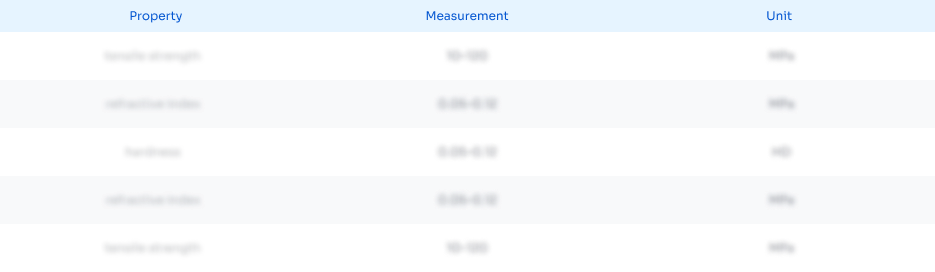
Abstract
Description
Claims
Application Information

- Generate Ideas
- Intellectual Property
- Life Sciences
- Materials
- Tech Scout
- Unparalleled Data Quality
- Higher Quality Content
- 60% Fewer Hallucinations
Browse by: Latest US Patents, China's latest patents, Technical Efficacy Thesaurus, Application Domain, Technology Topic, Popular Technical Reports.
© 2025 PatSnap. All rights reserved.Legal|Privacy policy|Modern Slavery Act Transparency Statement|Sitemap|About US| Contact US: help@patsnap.com