Low-nitrogen combustion device without primary air and secondary air, and application method
A low-nitrogen combustion and secondary air technology, applied in the combustion method, the use of multiple fuel combustion, the use of block fuel and liquid fuel combustion, etc., can solve the problem of high NOx emission concentration in boilers, and achieve lower emission concentration and combustion. The effect of widening the space adjustment space and reducing NOx
- Summary
- Abstract
- Description
- Claims
- Application Information
AI Technical Summary
Problems solved by technology
Method used
Image
Examples
specific Embodiment approach 1
[0022] Specific implementation mode one: combine figure 1 and figure 2 Describe this embodiment. This embodiment includes a bottom air nozzle 3, a compact overburning air nozzle 4, a lower separated overburning air nozzle 5, an upper separated overburning air nozzle 6, an oiling secondary air nozzle 2, an oil lowering Secondary air nozzle 13 and at least three primary air nozzles 1, upper separated overburning air nozzle 6, lower separated overburning air nozzle 5, compact overburning air nozzle 4, oiling secondary air nozzle 2, at least three A continuous arrangement of the primary air spout 1, the secondary air spout 13 and the bottom air spout 3 are arranged sequentially from top to bottom, the middle of the primary air spout 1 is vertically provided with a partition 12, and the middle of the primary air spout 1 The blunt body 10 is horizontally arranged, and the upper and lower spouts on the right side of the blunt body 10 are thick coal powder primary air spouts 7, and ...
specific Embodiment approach 2
[0023] Specific implementation mode two: combination figure 2 The present embodiment will be described. The ratio of the height H to the width B of the primary air nozzle 1 in the present embodiment is 1.2 to 1.5. When the primary air rate is high, increase the area of the primary air nozzle without increasing the lateral distance of the primary air nozzle 1 installation channel (without damaging the original water wall), and control the actual primary wind speed at 24m / s~30m / s. At the same time, a large-area peripheral air nozzle on the backfire side can be set to ensure that the primary air jet does not hit the wall. Other components and connections are the same as those in the first embodiment.
specific Embodiment approach 3
[0024] Specific implementation mode three: combination figure 2 Describe this embodiment, the peripheral wind 9 on the side of the primary air nozzle 8 of the light pulverized coal in this embodiment is the peripheral wind 9-1 on the backfire side, and the peripheral wind 9 on the primary air nozzle 7 side of the thick pulverized coal is the peripheral wind 9-1 on the fire side 2. The area of the perimeter wind 9-1 on the backfire side is 3 to 6 times the area of the perimeter wind 9-2 on the fire side. Other components and connections are the same as those in the second embodiment.
PUM
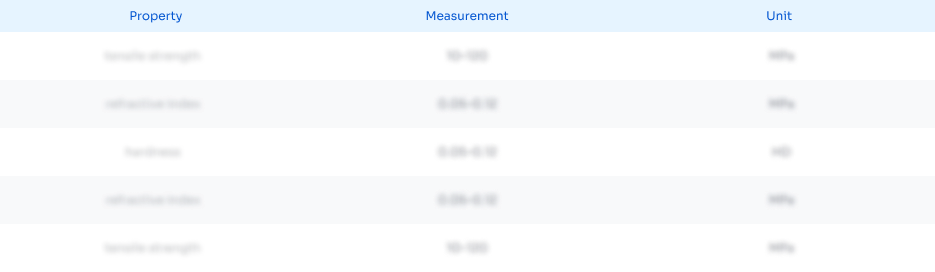
Abstract
Description
Claims
Application Information

- R&D
- Intellectual Property
- Life Sciences
- Materials
- Tech Scout
- Unparalleled Data Quality
- Higher Quality Content
- 60% Fewer Hallucinations
Browse by: Latest US Patents, China's latest patents, Technical Efficacy Thesaurus, Application Domain, Technology Topic, Popular Technical Reports.
© 2025 PatSnap. All rights reserved.Legal|Privacy policy|Modern Slavery Act Transparency Statement|Sitemap|About US| Contact US: help@patsnap.com