Method for recovering hydrogen and ammonia in synthetic ammonia exhausted gas
A technology for synthesizing ammonia degassing and hydrogen, applied in the direction of ammonia preparation/separation, hydrogen separation, hydrogen separation using solid contact, etc., can solve the problems of irreversible and damaged downstream separation membranes, and reduce energy consumption and operating costs , the effect of reducing land occupation
- Summary
- Abstract
- Description
- Claims
- Application Information
AI Technical Summary
Problems solved by technology
Method used
Image
Examples
Embodiment 1
[0026] exist figure 1 In the process schematic diagram of the method example 1 for recovering hydrogen and ammonia in the synthetic ammonia purge gas shown, the synthetic ammonia purge gas discharged by the synthesis system has a discharge pressure of 13MPa, a temperature of 26°C, and a gas volume of 12000Nm3 / hr. as follows:
[0027] components
[0028] The purge gas first enters the filter 1 to remove solid particles and liquid droplets that may be entrained by the air flow, and the filtered impurities are discharged from the bottom of the filter 1. The filtered gas passes through the first-stage heat exchanger 2, exchanges heat with the trapped gas of the second-stage separation membrane, raises the temperature of the gas to 41.8°C, and then passes through the second-stage heat exchanger 3 to separate from the first stage The heat exchange of the permeated gas of the membrane raises the temperature of the gas to 47.5°C, and then passes through the third-stage heat...
Embodiment 2
[0040] exist figure 2 In the process schematic diagram of the method example 2 of the shown recovery of hydrogen and ammonia in the synthetic ammonia purge gas, the synthetic ammonia purge gas discharged by the synthesis system has a discharge pressure of 12.3MPa, a temperature of 25°C, and a gas volume of 8000Nm3 / hr. The composition is as follows:
[0041] components
H 2
N 2
CH 4
Ar
NH 3
Content% (V / V)
63.00
21.84
8.10
3.55
3.50
[0042] The purge gas first enters the filter 1 to remove solid particles and liquid droplets that may be entrained by the air flow, and the filtered impurities are discharged from the bottom of the filter 1. The filtered gas passes through the first-stage heat exchanger 2, exchanges heat with the trapped gas separated by the membrane, raises the temperature of the gas to 37.68°C, and then passes through the second-stage heat exchanger 3, exchanges heat with the permeated gas separa...
PUM
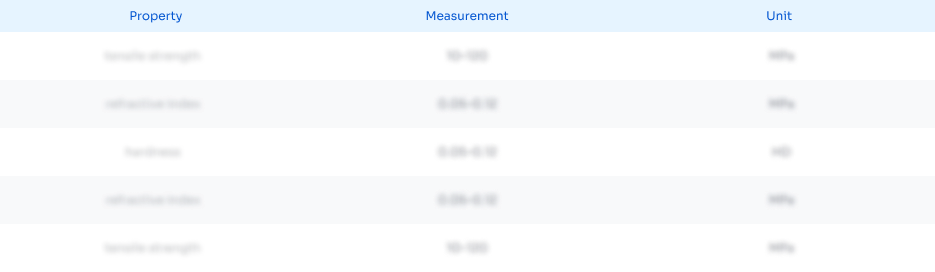
Abstract
Description
Claims
Application Information

- Generate Ideas
- Intellectual Property
- Life Sciences
- Materials
- Tech Scout
- Unparalleled Data Quality
- Higher Quality Content
- 60% Fewer Hallucinations
Browse by: Latest US Patents, China's latest patents, Technical Efficacy Thesaurus, Application Domain, Technology Topic, Popular Technical Reports.
© 2025 PatSnap. All rights reserved.Legal|Privacy policy|Modern Slavery Act Transparency Statement|Sitemap|About US| Contact US: help@patsnap.com