Drag-link mechanism of injection molding machine
A tie rod mechanism and injection molding machine technology, applied in the tie rod mechanism field, can solve the problems of tie rod fatigue, failure, badness, etc., and achieve the effect of weakening the influence of the force on the annular surface, flexible and controllable position and degree, and protecting the threaded section.
- Summary
- Abstract
- Description
- Claims
- Application Information
AI Technical Summary
Problems solved by technology
Method used
Image
Examples
Embodiment Construction
[0026] The present invention will be further described below in conjunction with the embodiments of the accompanying drawings.
[0027] Such as figure 1 As shown, the head of the tie rod 1 of the injection molding machine is provided with a threaded section 19 , and the front and rear areas adjacent to the threaded section 19 are provided with a fulcrum section 17 and a fulcrum section 18 .
[0028] An undercut 20 is also provided between the fulcrum section 17 and the threaded section 19 to facilitate processing.
[0029] The fulcrum section 17, the fulcrum section 18, the undercut 20 and the threaded section 19 are coaxial.
[0030] The pull rod 1 is also provided with an unloading groove 3 to control the bending of the pull rod 1 through its shape and position.
[0031] Such as figure 2 As shown, a support sleeve section 11 is arranged in front of the nut internal thread section 12 , and a support sleeve section 16 is provided behind the nut internal thread section 12 ....
PUM
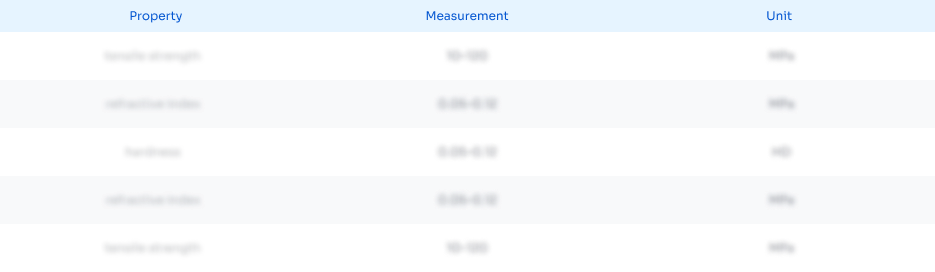
Abstract
Description
Claims
Application Information

- R&D
- Intellectual Property
- Life Sciences
- Materials
- Tech Scout
- Unparalleled Data Quality
- Higher Quality Content
- 60% Fewer Hallucinations
Browse by: Latest US Patents, China's latest patents, Technical Efficacy Thesaurus, Application Domain, Technology Topic, Popular Technical Reports.
© 2025 PatSnap. All rights reserved.Legal|Privacy policy|Modern Slavery Act Transparency Statement|Sitemap|About US| Contact US: help@patsnap.com