Single degree of freedom active magnetic bearing support vector machine self-adaption inverse controller construction method
A technology of support vector machine and active magnetic bearing, applied in adaptive control, general control system, control/regulation system, etc.
- Summary
- Abstract
- Description
- Claims
- Application Information
AI Technical Summary
Problems solved by technology
Method used
Image
Examples
Embodiment Construction
[0025] The concrete implementation of the present invention divides following 6 steps:
[0026] 1. If figure 1 As shown, the force-to-current converter 1, switching power amplifier 2, single-degree-of-freedom active magnetic bearing 3, eddy current displacement sensor 4 and displacement interface circuit 5 are taken as a whole to form a composite controlled object 6, and its input is axial suspension Force given signal The output is the axial displacement signal z;
[0027] 2. The axial suspension force signal F z (k) Applied to the input end of the composite controlled object 6, and collect the input axial suspension force signal F of the composite controlled object 6 at different times z (k), F z (k-1), and its output axial displacement signals z(k-1), z(k-2), z(k-3) at different times are used as the input of the support vector machine, and the composite controlled object is collected at 6k times The output axial displacement signal signal z(k) is the output of the su...
PUM
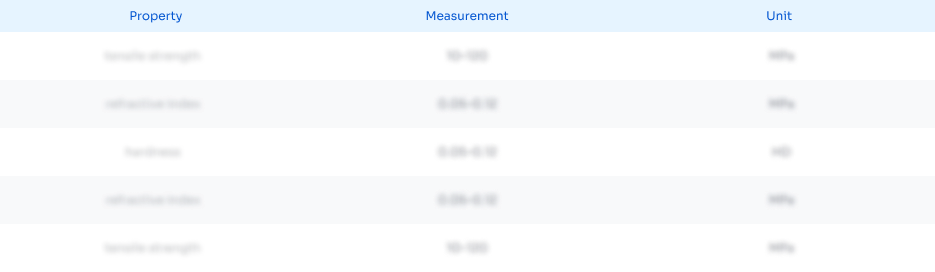
Abstract
Description
Claims
Application Information

- R&D
- Intellectual Property
- Life Sciences
- Materials
- Tech Scout
- Unparalleled Data Quality
- Higher Quality Content
- 60% Fewer Hallucinations
Browse by: Latest US Patents, China's latest patents, Technical Efficacy Thesaurus, Application Domain, Technology Topic, Popular Technical Reports.
© 2025 PatSnap. All rights reserved.Legal|Privacy policy|Modern Slavery Act Transparency Statement|Sitemap|About US| Contact US: help@patsnap.com