Composite material tower drum of wind driven generator as well as preparation method and preparation mold of composite material tower drum
A technology of wind turbines and composite materials, applied in wind turbine components, wind engines, wind power generation, etc., which can solve the problems of rusty casing and short life, and achieve the effects of reduced maintenance costs, light weight, and reduced transportation costs
- Summary
- Abstract
- Description
- Claims
- Application Information
AI Technical Summary
Problems solved by technology
Method used
Image
Examples
Embodiment 1
[0028] Embodiment 1: Prepare a 60m-high conical tower, which is formed by connecting 3 sections
[0029] Such as figure 1 As shown, the skin 1 and 25 stringers 2 are formed by co-curing, the 25 stringers 2 are evenly distributed on the inner surface of the skin 1, and the ordinary partition frames 3 are evenly distributed along the height direction of the tower and perpendicular to the stringer 2 Install. The long stringer 2 is "Ω" shape, and the bulkhead 3 is "C" shape.
[0030] Such as figure 2 As shown in , the mold 4 has 25 evenly distributed "Ω"-shaped grooves 5, and the rotating shaft 6 of the mold 4 can rotate and move axially. The raw materials are: glass fiber, epoxy resin, PVC foam, quartz sand. The common partition frame 3 is pre-prepared by a compression molding process. The connection frame 9 is made of metal materials, as shown in FIG. 5 .
[0031] The preparation method comprises the following steps:
Embodiment 2
[0036] Prepare a 100m-high conical tower, which is connected by 5 sections. The difference from Example 1 is that the skin 1 is reinforced by mixing glass fiber and carbon fiber, the stringer core of the stringer 2 is made of balsa wood, and the ordinary frame 3 is made of "L" shaped frame.
PUM
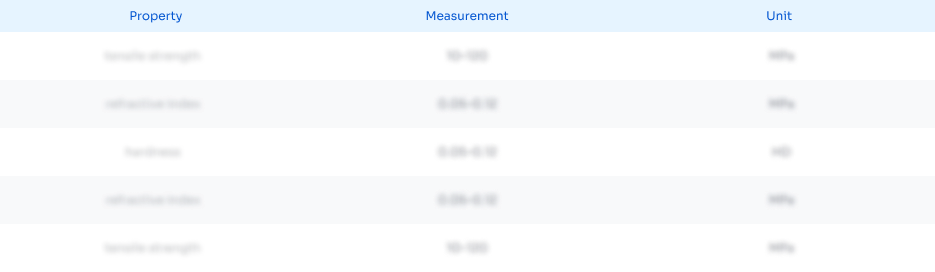
Abstract
Description
Claims
Application Information

- R&D Engineer
- R&D Manager
- IP Professional
- Industry Leading Data Capabilities
- Powerful AI technology
- Patent DNA Extraction
Browse by: Latest US Patents, China's latest patents, Technical Efficacy Thesaurus, Application Domain, Technology Topic, Popular Technical Reports.
© 2024 PatSnap. All rights reserved.Legal|Privacy policy|Modern Slavery Act Transparency Statement|Sitemap|About US| Contact US: help@patsnap.com