Combined non-spill drain baffle
A leak-free, baffle technology, applied in liquid fuel engines, oscillating piston machinery, machines/engines, etc., can solve the problem of difficult to block gas backflow, low discharge pressure and volumetric efficiency of oscillating pumps, and limited application range of oscillating rotor pumps, etc. problem, to achieve the effect of enhanced impact resistance, convenient installation and maintenance, and reduced radial size
- Summary
- Abstract
- Description
- Claims
- Application Information
AI Technical Summary
Problems solved by technology
Method used
Image
Examples
Embodiment 1
[0026] Embodiment 1, Figure 1 to Figure 4 A combined non-leakage drain partition is given, including the drain partition 1, the roller 2 and the rectangular diaphragm 3; the drain partition 1 is provided with a drain channel 6 (the number of the drain channel 6 can be determined according to the pump Choose the size of the pump, if the pump is large, you can set multiple discharge channels 6, if the pump is small, you can set at least one discharge channel 6), such as figure 2 As shown, in this embodiment, four drainage channels 6 are used, and reinforcing ribs 7 are provided between any adjacent two drainage channels 6. If the number of drainage channels 6 exceeds one, you can set Ribs 7 are used to ensure the rigidity of the drainage channel 6 . Corresponding cylindrical channel 8 is set at the lower end of the liquid discharge partition 1 (cylindrical channel 8 is set corresponding to the cylindrical groove of the swing pump rotor. Generally, the swing pump rotor has cyl...
PUM
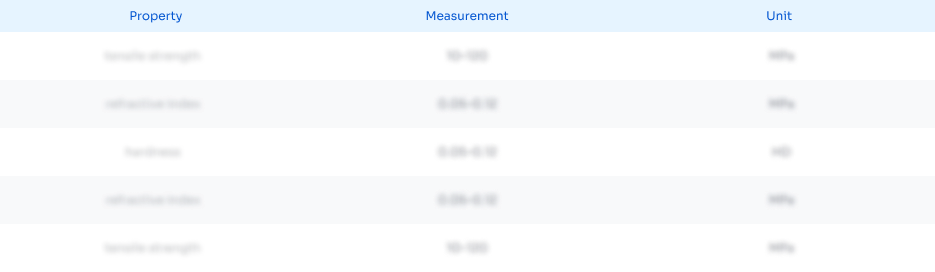
Abstract
Description
Claims
Application Information

- R&D
- Intellectual Property
- Life Sciences
- Materials
- Tech Scout
- Unparalleled Data Quality
- Higher Quality Content
- 60% Fewer Hallucinations
Browse by: Latest US Patents, China's latest patents, Technical Efficacy Thesaurus, Application Domain, Technology Topic, Popular Technical Reports.
© 2025 PatSnap. All rights reserved.Legal|Privacy policy|Modern Slavery Act Transparency Statement|Sitemap|About US| Contact US: help@patsnap.com