Preparation method of amphiphilic fluorine-containing nanoparticle/fluorine-containing epoxy resin hybrid and application thereof
An epoxy resin and nano-microsphere technology, applied in epoxy resin coatings, nanotechnology, nanotechnology and other directions, can solve the problems of high cost, weak adhesion, high requirements on reagents and equipment, etc. The effect of scrubbing and corrosion resistance
- Summary
- Abstract
- Description
- Claims
- Application Information
AI Technical Summary
Problems solved by technology
Method used
Image
Examples
Embodiment 1
[0048] (1) Preparation of amphiphilic fluorine-containing nanospheres / fluorine-containing epoxy resin hybrids:
[0049] (1) Disperse microspheres A in solvent B, sonicate (ultrasonic power 100W, temperature 35°C) for 0.5h, then place in an oil bath at 80°C and stir at a stirring speed of 100rpm, Add epoxy resin C and catalyst D dropwise to the above system (the drop rate is 0.5g / min). Place the above system in a vacuum oven at 100°C and bake for 0.5 hours to obtain a hybrid of microspheres and epoxy resin grafted with epoxy groups on the surface;
[0050] Wherein the mass ratio of microsphere A, solvent B, epoxy resin C and catalyst D is 1:10:2:0; the microsphere is silica, and its particle size is 100nm; epoxy resin C is poly Glycidyl methacrylate, its molecular weight is 50000; Solvent B is dimethyl sulfoxide; Catalyst D is imidazole;
[0051] (2) Dissolve the microspheres grafted with epoxy groups on the surface obtained in step (1) and the epoxy resin hybrid in solvent E...
Embodiment 2
[0060] (1) Preparation of amphiphilic fluorine-containing nanospheres / fluorine-containing epoxy resin hybrids:
[0061] (1) Disperse microspheres A in solvent B, sonicate (ultrasonic power 500W, temperature 70°C) for 2 hours, then place in an oil bath at 120°C, stir at a stirring speed of 500rpm, Add epoxy resin C and catalyst D dropwise to the above-mentioned system (the drop rate is 10g / min). The above system was placed in a vacuum oven at 150°C and baked for 2 hours to obtain a hybrid of microspheres with epoxy groups grafted on the surface and epoxy resin;
[0062] Among them, the mass ratio of microsphere A, solvent B, epoxy resin C and catalyst D is 1:100:20:0.0001; the microsphere is titanium dioxide microsphere, and its particle size is 1000nm; epoxy resin C is polymethacrylic acid Glycidyl ester, its molecular weight is 20000; Solvent B is butanone; Catalyst D is diisopropyl ethylamine;
[0063] (2) Dissolve the hybrid of microspheres grafted with epoxy groups on th...
Embodiment 3
[0071] (1) Preparation of amphiphilic fluorine-containing nanospheres / fluorine-containing epoxy resin hybrids:
[0072] (1) Disperse the microspheres A in the solvent B, sonicate (ultrasonic power 300W, temperature 60°C) for 1h, then place in an oil bath at a temperature of 110°C and stir at a stirring speed of 500rpm, and then Add epoxy resin C and catalyst D dropwise to the above system (the drop rate is 2g / min). The system was placed in a vacuum oven at 120°C and baked for 1.5 hours to obtain a hybrid of microspheres and epoxy resin grafted with epoxy groups on the surface;
[0073] The mass ratio of microsphere A, solvent B, epoxy resin C and catalyst D is 1:80:10:0.00001; described microsphere is polystyrene microsphere, and its particle size is 100nm; Epoxy resin C is Novolak epoxy resin, its molecular weight is 20000; Solvent B is dimethyl sulfoxide; Catalyst D is oleyl dimethyl tertiary amine;
[0074] (2) Dissolve the microspheres grafted with epoxy groups on the su...
PUM
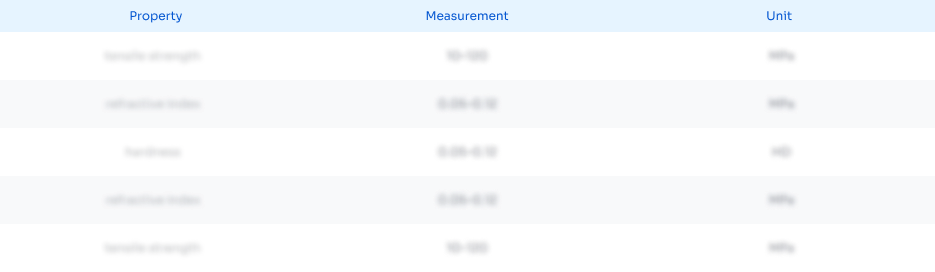
Abstract
Description
Claims
Application Information

- R&D
- Intellectual Property
- Life Sciences
- Materials
- Tech Scout
- Unparalleled Data Quality
- Higher Quality Content
- 60% Fewer Hallucinations
Browse by: Latest US Patents, China's latest patents, Technical Efficacy Thesaurus, Application Domain, Technology Topic, Popular Technical Reports.
© 2025 PatSnap. All rights reserved.Legal|Privacy policy|Modern Slavery Act Transparency Statement|Sitemap|About US| Contact US: help@patsnap.com