Brushless direct-current motor simulator
A DC motor and simulator technology, applied in the direction of electronic commutation motor control, electrical components, control systems, etc., can solve the problems of equipment performance degradation, affecting flywheel safety, high price, etc., to achieve protection safety, convenient transportation, and easy operation. Effect
- Summary
- Abstract
- Description
- Claims
- Application Information
AI Technical Summary
Problems solved by technology
Method used
Image
Examples
Embodiment
[0063] The present invention adopts TI company's DSP-TMS320F28335 with a floating-point core as the CPU to complete the relevant calculation of the motor model; use the integrated AD converter to sample the output of the current sensor; use the integrated PWM module to cooperate with low-pass filtering The device completes the DA conversion output of the back EMF control signal; uses the IO port peripheral to control the work of the relay, and cuts off the connection between the three-phase analog winding of the brushless DC motor simulator and the electrical interface when an abnormality such as overcurrent is detected; also uses the IO port peripheral Combined with the timer to control the OC gate to simulate the output of the Hall position sensor. The invention uses Honeywell's current transformer to detect the three-phase winding current, and converts it into a voltage signal output, which is processed by low-pass filtering and biasing for AD sampling. The invention adopts...
PUM
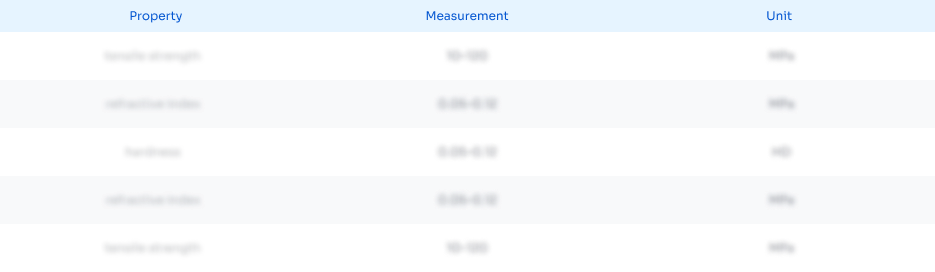
Abstract
Description
Claims
Application Information

- R&D
- Intellectual Property
- Life Sciences
- Materials
- Tech Scout
- Unparalleled Data Quality
- Higher Quality Content
- 60% Fewer Hallucinations
Browse by: Latest US Patents, China's latest patents, Technical Efficacy Thesaurus, Application Domain, Technology Topic, Popular Technical Reports.
© 2025 PatSnap. All rights reserved.Legal|Privacy policy|Modern Slavery Act Transparency Statement|Sitemap|About US| Contact US: help@patsnap.com