Compound stress environment testing system of contact point material
A technology that integrates stress and environmental experiments, applied in the direction of testing wear resistance, etc., can solve the problems of inability to complete the detection of fretting wear performance, failure of electrical connectors, etc., to achieve the effect of stable work and improved detection accuracy
- Summary
- Abstract
- Description
- Claims
- Application Information
AI Technical Summary
Problems solved by technology
Method used
Image
Examples
specific Embodiment approach 1
[0029] Specific implementation mode one, combination figure 1 , figure 2 with image 3 To illustrate this specific embodiment, the contact material comprehensive stress environment experiment system described in this specific embodiment includes a vacuum chamber, a micro-movement clamping mechanism, a fixed clamping mechanism and a control circuit,
[0030] The vacuum chamber is composed of a chassis 11 and a vacuum cover 20. The vacuum cover 20 is fixedly connected to the chassis 11 and forms a closed space with the chassis 11, the space being a vacuum chamber; the chassis 11 is provided with a sealed aviation plug-in 18. Pressure transmitter installation through hole, air valve installation through hole and fixed clamping mechanism installation through hole;
[0031] The micro-movement clamping mechanism is located in the vacuum chamber, and the micro-movement clamping mechanism is fixed at the center of the chassis 11. The micro-movement clamping mechanism is composed of a lower...
specific Embodiment approach 2
[0043] Specific embodiment two, the difference between this specific embodiment and the contact material comprehensive stress environment experiment system described in specific embodiment one is that the chassis 11 and the vacuum cover 20 are sealed by a silicone gasket, and the chassis 11 and the vacuum cover 20 is fixedly connected by a plurality of C-type clamps 21.
specific Embodiment approach 3
[0044] Embodiment 3 The difference between this embodiment and the contact material comprehensive stress environment experiment system described in embodiment 1 is that it also includes a gas valve 17 fixedly installed in the valve installation through hole One end of the air valve 17 is connected to the vacuum chamber, and the other end of the air valve 17 is connected to the suction port of the vacuum pump 38.
PUM
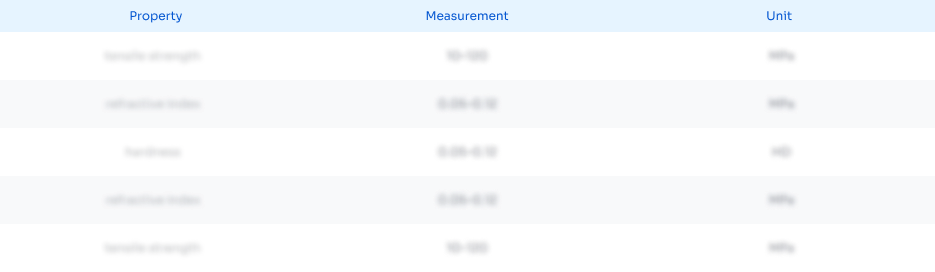
Abstract
Description
Claims
Application Information

- R&D Engineer
- R&D Manager
- IP Professional
- Industry Leading Data Capabilities
- Powerful AI technology
- Patent DNA Extraction
Browse by: Latest US Patents, China's latest patents, Technical Efficacy Thesaurus, Application Domain, Technology Topic, Popular Technical Reports.
© 2024 PatSnap. All rights reserved.Legal|Privacy policy|Modern Slavery Act Transparency Statement|Sitemap|About US| Contact US: help@patsnap.com