Medium oil alkyd resin for preparing matt resin and preparation method of medium oil alkyd resin
An alkyd resin and matte resin technology, used in coatings, polyester coatings, etc., can solve the problems of high temperature baking, high cost, poor flexibility, etc., and achieve the effect of large construction scope and cost reduction.
- Summary
- Abstract
- Description
- Claims
- Application Information
AI Technical Summary
Problems solved by technology
Method used
Image
Examples
Embodiment 1
[0025] (1) Resin formula
[0026]
[0027] (2) Preparation steps
[0028] According to the production volume, choose equipment and tools such as dispersing cylinder and dispersing machine, and choose the power of the machine. In principle, the higher the power, the easier it is to disperse the material, and make sure it is clean and trouble-free.
[0029] (1) Put trimethylolpropane, phthalic anhydride, castor oil and 2.42kg xylene (for reflux) into the reaction pot, raise the temperature to about 107°C-113°C and start stirring, adjust the stirring speed to 200-400r / min, to 150-160 Reflux at ℃, discharge water, keep warm at 230-240℃;
[0030] (2) After measuring the acid value of 23KOHmg / g according to the water separator and the outlet water, the temperature is rapidly raised to 260-265°C and kept for 30 minutes;
[0031] (3) Rapidly cool to 230°C and measure the acid value of 13KOHmg / g, then continue to cool down to 90°C, then dilute with the remaining xylene and 1000# s...
Embodiment 2
[0033] (1) Resin formula
[0034]
[0035] (2) Preparation steps
[0036] According to the production volume, choose equipment and tools such as dispersing cylinders and dispersing machines, and choose the power of the machine. In principle, the higher the power, the easier it is to disperse the material, and make sure it is clean and trouble-free.
[0037] (1) Put trimethylolpropane, phthalic anhydride, castor oil and 2.42kg xylene (for reflux) into the reaction pot, raise the temperature to 107°C-113°C and start stirring, adjust the stirring speed to 200-400r / min, to 150-160°C Reflux, release water, keep warm at 230-240°C;
[0038] (2) After measuring the acid value of 24KOHmg / g according to the water separator and the outlet water, the temperature is rapidly raised to 260-265°C and kept for 30 minutes;
[0039] (3) Rapidly cool to 230°C and measure the acid value of 13KOHmg / g, then continue to cool down to 90°C, then dilute with the remaining xylene and 1000# solvent o...
Embodiment 3
[0041] (1) Resin formula
[0042]
[0043] (2) Preparation steps
[0044] According to the production volume, choose equipment and tools such as dispersing cylinders and dispersing machines, and choose the power of the machine. In principle, the higher the power, the easier it is to disperse the material, and make sure it is clean and trouble-free.
[0045] (1) Put trimethylolpropane, phthalic anhydride, castor oil and 2.42kg xylene (for reflux) into the reaction pot, heat up to 107°C-113°C and start stirring, adjust the stirring speed to 200-400r / min, to 150-160 Reflux at ℃, discharge water, keep warm at 230-240℃;
[0046] (2) After measuring the acid value of 23KOHmg / g according to the water separator and the outlet water, the temperature is rapidly raised to 260-265°C and kept for 30 minutes;
[0047] (3) Rapidly cool to 230°C and measure the acid value to 12.8KOHmg / g, then continue to cool down to 90°C, and dilute with xylene and 1000#. Sampling to measure the viscos...
PUM
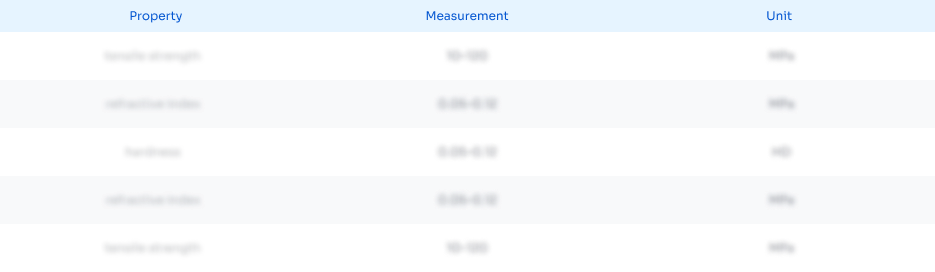
Abstract
Description
Claims
Application Information

- R&D
- Intellectual Property
- Life Sciences
- Materials
- Tech Scout
- Unparalleled Data Quality
- Higher Quality Content
- 60% Fewer Hallucinations
Browse by: Latest US Patents, China's latest patents, Technical Efficacy Thesaurus, Application Domain, Technology Topic, Popular Technical Reports.
© 2025 PatSnap. All rights reserved.Legal|Privacy policy|Modern Slavery Act Transparency Statement|Sitemap|About US| Contact US: help@patsnap.com