Plate material multi-point-die pre-drawing progressive compound forming method and plate material multi-point-die pre-drawing progressive compound forming device
A composite forming and incremental forming technology, applied in the field of material incremental forming, can solve the problems such as the difficulty of constraining and controlling the dimensional accuracy of parts, the complex flow and stress state of the sheet metal, and the difficulty in ensuring the uniformity of thickness distribution, so as to overcome the problems of sheet thickness distribution. Uneven, high forming efficiency, time saving effect
- Summary
- Abstract
- Description
- Claims
- Application Information
AI Technical Summary
Problems solved by technology
Method used
Image
Examples
Embodiment
[0034] Such as Figure 1-Figure 4 As shown, a sheet metal multi-point die pre-drawing progressive composite forming device, including a base plate 1, a back pressure component, a mold seat 3, a lifting cylinder 4, a rotary clamping structure, a multi-point die 8, and a guide column 10 , drawing workbench 11, vertical support 14, six-degree-of-freedom motion mechanism 16 and tool head 17, described back pressure assembly, lifting oil cylinder 4, guide column 10 and mold seat 3 are all fixed on the base plate 1; Described The drawing table 11 is respectively connected to the lifting cylinder 4 and the guide column 10; the multi-point mold 8 is arranged on the mold base 3 and is located under the drawing table 4; the described back pressure assembly passes through the mold base 3 and The rotary clamping structure is connected; the rotary clamping structure is arranged on the drawing table 11; the vertical support 14 is vertically connected to one end of the base plate 1; the tool...
PUM
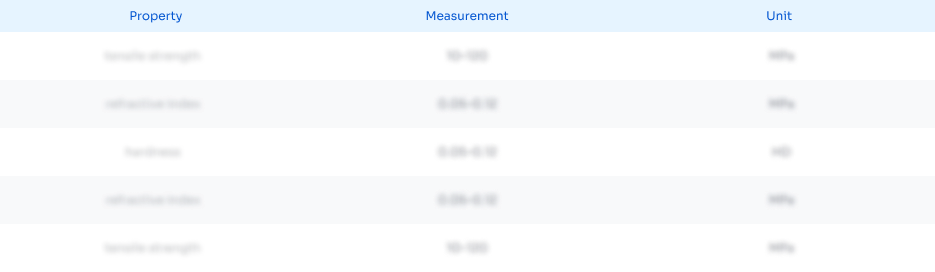
Abstract
Description
Claims
Application Information

- R&D
- Intellectual Property
- Life Sciences
- Materials
- Tech Scout
- Unparalleled Data Quality
- Higher Quality Content
- 60% Fewer Hallucinations
Browse by: Latest US Patents, China's latest patents, Technical Efficacy Thesaurus, Application Domain, Technology Topic, Popular Technical Reports.
© 2025 PatSnap. All rights reserved.Legal|Privacy policy|Modern Slavery Act Transparency Statement|Sitemap|About US| Contact US: help@patsnap.com