Method for automatically compensating pose errors in machining process of optical element
An optical element and automatic compensation technology, which is applied in the direction of instruments, computer control, simulators, etc., can solve the problems of large-caliber optical elements, laborious adjustment process, time-consuming adjustment process, cumbersome adjustment process, etc., to achieve fast compensation process, short time consumption, The effect of narrowing your search
- Summary
- Abstract
- Description
- Claims
- Application Information
AI Technical Summary
Problems solved by technology
Method used
Image
Examples
Embodiment Construction
[0042] Below in conjunction with accompanying drawing and specific embodiment the present invention is described in further detail:
[0043] The method for automatically compensating pose error in optical element processing of the present invention comprises the following steps:
[0044] (1) Clamp the optical element 1 on the workbench 3:
[0045] Such as figure 1 As shown, the optical element 1 is clamped on the vacuum adsorption fixture 2, the upper surface 11 of the optical element is the surface to be processed, and the lower surface 12 is the mounting and positioning surface. The lower surface 12 is in close contact with the suction surface 21 of the vacuum suction fixture 2 . The vacuum adsorption fixture 2 is fixedly installed on the machine tool table 3, and the two are in a coaxial relationship. Since the lower surface 12 of the optical element 1 is a spherical surface, the optical element 1 will produce certain tilt errors and translation errors. When clamping th...
PUM
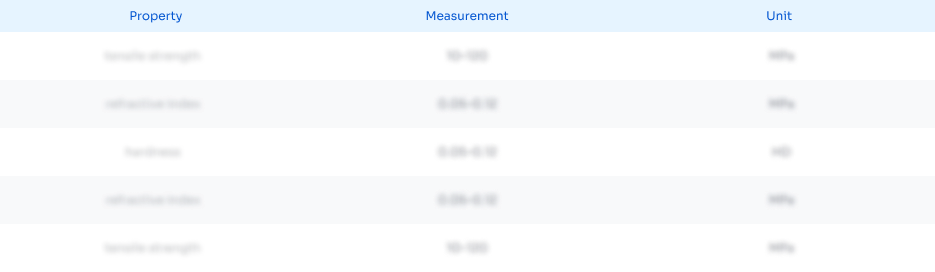
Abstract
Description
Claims
Application Information

- R&D
- Intellectual Property
- Life Sciences
- Materials
- Tech Scout
- Unparalleled Data Quality
- Higher Quality Content
- 60% Fewer Hallucinations
Browse by: Latest US Patents, China's latest patents, Technical Efficacy Thesaurus, Application Domain, Technology Topic, Popular Technical Reports.
© 2025 PatSnap. All rights reserved.Legal|Privacy policy|Modern Slavery Act Transparency Statement|Sitemap|About US| Contact US: help@patsnap.com