Burner of direct-injection type cooker combustor
A burner, direct injection technology, applied in the direction of burner, gas fuel burner, combustion method, etc., can solve the problems of waste gas, low power, insufficient gas combustion, etc.
- Summary
- Abstract
- Description
- Claims
- Application Information
AI Technical Summary
Problems solved by technology
Method used
Image
Examples
Embodiment 1
[0027] Such as figure 1 , figure 2 As shown, a burner head of a direct-injection stove burner includes a burner body 1 and a nozzle 2. The burner body 1 has an outer ring gas mixture chamber 11, a central air intake pipe 12 and a premix chamber 13. The ring mixing chamber 11 and the premixing chamber 13 communicate through the air guide hole 15 on the partition 14; the lower end of the central air intake pipe 12 is fixedly connected with the central air intake hole 141 on the partition 14, and the air guide hole 15 surrounds the central air intake Hole 141, the lower end of the central air intake pipe 12 communicates with the premix chamber 13 through the central air intake hole 141; the nozzle 2 is opposite to the central air intake hole 141 and the air guide hole 15; the burner body 1 is integrally formed.
[0028] The upper end area of the air guide hole 15 is small and the lower end area is large, that is to say: the air guide hole 15 is in the shape of a truncated con...
Embodiment 2
[0041] Such as Figure 4 shown, refer to figure 1 As shown, a burner head of a direct-injection cooker burner includes a burner body 1 and a nozzle 2. The burner body has a mixed gas cavity 11, a central air intake pipe 12 and a premixed cavity 13. The mixed gas cavity 11 It communicates with the premixing chamber 13 through the air guide hole 15 on the partition 14; the lower end of the central air intake pipe 12 is fixedly connected with the central air intake hole 141 on the partition plate, and the air guide hole 15 surrounds the central air intake hole 141, and the central air intake pipe The lower end of 12 communicates with the premix chamber 13; the nozzle 2 is opposite to the central air inlet 141 and the air guide hole 15; the number of the mixed air chamber 11 matches the number of the air guide hole 15;
[0042] The lower end of the air guide hole 15 has a compression chamber, which is in the shape of a truncated cone.
PUM
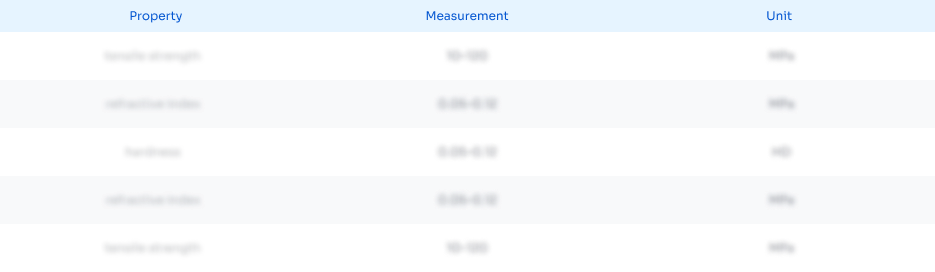
Abstract
Description
Claims
Application Information

- R&D
- Intellectual Property
- Life Sciences
- Materials
- Tech Scout
- Unparalleled Data Quality
- Higher Quality Content
- 60% Fewer Hallucinations
Browse by: Latest US Patents, China's latest patents, Technical Efficacy Thesaurus, Application Domain, Technology Topic, Popular Technical Reports.
© 2025 PatSnap. All rights reserved.Legal|Privacy policy|Modern Slavery Act Transparency Statement|Sitemap|About US| Contact US: help@patsnap.com