Method for producing computer cross-stitch printed and dyed cloth
A production method, cross-stitch technology, applied in dyeing, textile material processing, textile material inspection, etc., can solve the problems of computer "cross-stitch production interruption, computer cannot correct recognition, mesh grid displacement, etc. To achieve the effect of enhancing the anti-weft shifting effect, high strength, and preventing the decline of strength
- Summary
- Abstract
- Description
- Claims
- Application Information
AI Technical Summary
Problems solved by technology
Method used
Examples
Embodiment 1
[0039] The production method of computerized cross-stitch printing and dyeing fabric includes the following steps in turn: fabric turning, weft yarn cutting, seaming, singeing, descouring and bleaching, mercerizing, dyeing, weft adjustment, and tentering.
[0040] The front and back of the cloth are required to be consistent, the seam head is straight, and it is required to be flat, straight, neat, and firm. The needle density is 40 needles / 15cm, and the two sides are encrypted to 4 needles / cm to prevent wrinkles, weft skew, and curls during printing and dyeing. side. Weft yarn cutting is to cut the fabric according to the weft yarn; seam is to carry out parallel weft yarn sewing on the seams between machines and fabrics.
[0041] Singeing adopts gas singeing, and singes twice on the front of the two burners at a speed of 80m / min.
[0042] In descouring, bleaching, mercerizing and dyeing, the moisture content of the roll is kept consistent so as to reduce the weft displacemen...
Embodiment 2
[0057] The production method of computerized cross-stitch printing and dyeing fabric includes the following steps in turn: fabric turning, weft yarn cutting, seaming, singeing, descouring and bleaching, mercerizing, dyeing, weft adjustment, and tentering.
[0058] The front and back of the fabric are required to be consistent, the seam head is straight, and it is required to be flat, straight, neat, and firm. The needle density is 45 needles / 15cm, and the two sides are densely encrypted to 6 needles / cm to prevent wrinkles, weft skew, and curls during printing and dyeing. side. Weft yarn cutting is to cut the fabric according to the weft yarn; seam is to carry out parallel weft yarn sewing on the seams between machines and fabrics.
[0059] Singeing adopts gas singeing, and singes twice on the front of the two burners at a speed of 85m / min.
[0060] In descouring, bleaching, mercerizing and dyeing, the moisture content of the roll is kept consistent so as to reduce the weft di...
Embodiment 3
[0074] The production method of computerized cross-stitch printing and dyeing fabric includes the following steps in turn: fabric turning, weft yarn cutting, seaming, singeing, descouring and bleaching, mercerizing, dyeing, weft adjustment, and tentering.
[0075] The front and back of the cloth are required to be consistent, the seam head is straight, and it is required to be flat, straight, neat, and firm. The needle density is 42 needles / 15cm, and the two sides are encrypted to 5 needles / cm to prevent wrinkles, weft skew, and curls during printing and dyeing. side. Weft yarn cutting is to cut the fabric according to the weft yarn; seam is to carry out parallel weft yarn sewing on the seams between machines and fabrics.
[0076] Singeing adopts gas singeing, and singes twice on the front of the two burners at a speed of 83m / min.
[0077] In descouring, bleaching, mercerizing and dyeing, the moisture content of the roll is kept consistent so as to reduce the weft displacemen...
PUM
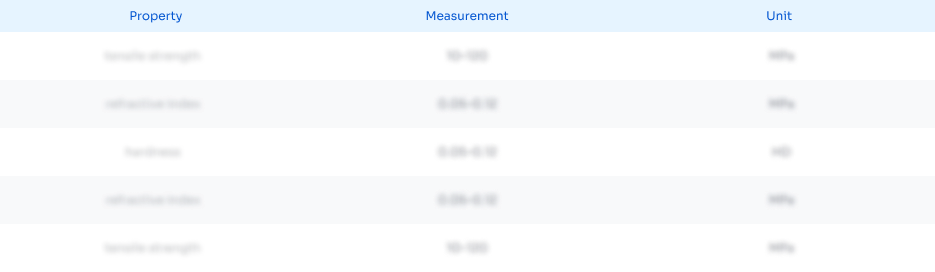
Abstract
Description
Claims
Application Information

- Generate Ideas
- Intellectual Property
- Life Sciences
- Materials
- Tech Scout
- Unparalleled Data Quality
- Higher Quality Content
- 60% Fewer Hallucinations
Browse by: Latest US Patents, China's latest patents, Technical Efficacy Thesaurus, Application Domain, Technology Topic, Popular Technical Reports.
© 2025 PatSnap. All rights reserved.Legal|Privacy policy|Modern Slavery Act Transparency Statement|Sitemap|About US| Contact US: help@patsnap.com