T/R yarn blending process
A process and yarn technology, which is applied in the field of T/R yarn blending process, can solve the problems of high energy consumption, large T/R yarn dyeing color difference, and low production process efficiency, so as to improve production efficiency and reduce dyeing color difference , the effect of improving customer satisfaction
- Summary
- Abstract
- Description
- Claims
- Application Information
AI Technical Summary
Problems solved by technology
Method used
Examples
Embodiment 1
[0026] A kind of T / R yarn blending technique, comprises following process step:
[0027] (1) Place the imitation Dahua polyester staple fiber and viscose fiber in the automatic cotton grabbing machine according to the ratio of 90% and 10% by weight. Mix with viscose fiber; Wherein, the spindle speed of the automatic plucking machine is 800rpm; The automatic catching machine is preferably a disc-type automatic catching machine;
[0028] (2) The automatic catching machine transports the mixed imitation Dahua polyester staple fiber and viscose fiber to the vibrating cotton box for opening, mixing, and processing into uniform cotton laps; among them, the vibration in the vibrating cotton box The vibration frequency of the plate is 160 times / min; the rotation speed of the cotton feeding roller is 6.45rpm;
[0029] (3) Transport the laps to the carding machine for opening, carding, dust removal and mixing to form a sliver; among them, the cotton layer weight is 600g / m; the spee...
Embodiment 2
[0035] A kind of T / R yarn blending technique, comprises following process step:
[0036] (1) Place the imitation Dahua polyester staple fiber and viscose fiber in the automatic cotton grabbing machine according to the ratio of 85% and 15% by weight. Mix with viscose fiber; Wherein, the spindle speed of the automatic plucking machine is 720rpm; The automatic catching machine is preferably a disc-type automatic catching machine;
[0037] (2) The automatic catching machine transports the mixed imitation Dahua polyester staple fiber and viscose fiber to the vibrating cotton box for opening, mixing, and processing into uniform cotton laps; among them, the vibration in the vibrating cotton box The vibration frequency of the plate is 82 times / min; the rotation speed of the cotton feeding roller is 4.75rpm;
[0038] (3) Transport the laps to the carding machine for opening, carding, dust removal and mixing to form sliver; among them, the basis weight of the cotton layer is 400g / m...
Embodiment 3
[0044] A kind of T / R yarn blending technique, comprises following process steps:
[0045] (1) Put the imitation Dahua polyester staple fiber and viscose fiber in the automatic cotton grabbing machine according to the ratio of 95% and 5% by weight. Mix with viscose fiber; Wherein, the spindle speed of the automatic plucking machine is 871rpm; The automatic catching machine is preferably a disc-type automatic catching machine;
[0046] (2) The automatic catching machine transports the mixed imitation Dahua polyester staple fiber and viscose fiber to the vibrating cotton box for opening, mixing, and processing into uniform cotton laps; among them, the vibration in the vibrating cotton box The vibration frequency of the plate is 205 times / min; the rotation speed of the cotton feeding roller is 7.45rpm;
[0047] (3) Transport the laps to the carding machine for opening, carding, dust removal and mixing to form sliver; among them, the basis weight of the cotton layer is 800g / m;...
PUM
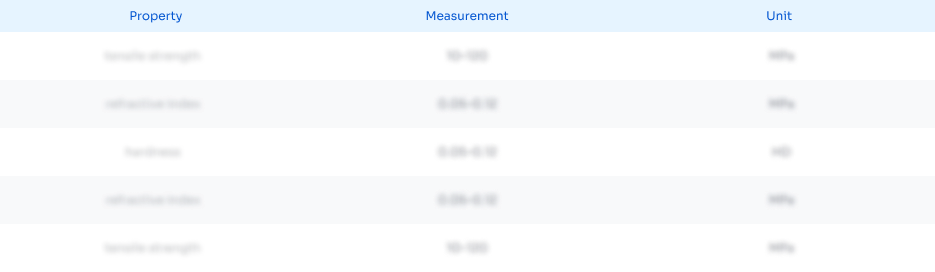
Abstract
Description
Claims
Application Information

- R&D
- Intellectual Property
- Life Sciences
- Materials
- Tech Scout
- Unparalleled Data Quality
- Higher Quality Content
- 60% Fewer Hallucinations
Browse by: Latest US Patents, China's latest patents, Technical Efficacy Thesaurus, Application Domain, Technology Topic, Popular Technical Reports.
© 2025 PatSnap. All rights reserved.Legal|Privacy policy|Modern Slavery Act Transparency Statement|Sitemap|About US| Contact US: help@patsnap.com