Process of utilizing wood plastic composite for manufacturing formaldehyde-free bending glued parts
A technology of wood-plastic composites and parts, which is applied in the direction of manufacturing tools, wood processing appliances, and the joining of wooden veneers. It can solve the problems of inability to make curved furniture parts, reduce the bending performance of veneers, and affect the environmental protection of furniture, etc. problems, to achieve the effect of improving the surface decoration effect, solving the problem of formaldehyde pollution, and low requirements for equipment and molds
- Summary
- Abstract
- Description
- Claims
- Application Information
AI Technical Summary
Problems solved by technology
Method used
Image
Examples
Embodiment 1
[0015] (1) Preparation of "C" type chair back curved parts: According to the large radius of curvature of the part (650 mm), select the Eucalyptus veneer, the thickness of the veneer is 1.5 mm, and the moisture content of the veneer is 10%. The glued surface is processed by rolling holes, the pores are irregularly distributed, and the number of pores is 20-30 / cm 2 Between, the veneer is cut into specifications length × width: 400 × 250mm;
[0016] (2) Cutting the prefabricated polyethylene plastic film to a size 2mm larger in width than the veneer;
[0017] (3) According to the part thickness of 15 mm, combined with the thickness of the veneer and plastic film and the compression rate of the pressing and bending process, the layers of 11 layers of veneer and 10 layers of plastic film are alternately stacked to form the billet. Both sides are veneer;
[0018] (4) Place the slab in a hard mold made of "C" type laminated lumber, use high-frequency heating to heat and pressu...
Embodiment 2
[0022] (1) Preparation of "L"-shaped chair back and seat integrated curved parts: According to the large radius of curvature of the part (100 mm), birch veneer is selected, the thickness of the veneer is 1.5 mm, and the moisture content of the veneer is 10%. And carry out rolling hole treatment on the veneer glued surface, the pores are irregularly distributed, and the number of pores is 20-30 / cm 2 , the veneer is cut into specifications length × width: 1000 × 400 mm;
[0023] (2) Cutting the prefabricated polyethylene plastic film to a size 2mm larger in width than the veneer;
[0024] (3) According to the part thickness of 15 mm, combined with the thickness of the veneer and plastic film and the compression rate of the pressing and bending process, the layers of 11 layers of veneer and 10 layers of plastic film are alternately stacked to form the billet. Both sides are veneer
[0025] (4) Place the slab in a hard mold made of "L"-shaped laminated lumber, use high-frequen...
Embodiment 3
[0029] (1) Preparation of curved parts of armrest of "U"-shaped leisure chair: According to the small curvature radius of the part (60 mm), choose ash veneer, the thickness of the veneer is 1.5 mm, and the moisture content of the veneer is 12%. The veneer glued surface is processed by rolling holes, the pores are irregularly distributed, and the number of pores is 20-30 / cm 2 Between, the veneer is cut into a specification length×width: 800×220 mm;
[0030] (2) Cutting the prefabricated polyethylene plastic film to a size 2mm larger than the average width of the veneer;
[0031] (3) According to the thickness of the part is 10 mm, combined with the thickness of the veneer, plastic film and the compression rate of the pressurization and bending process, the layers of 9 layers of veneer and 8 layers of plastic film are alternately stacked to form the billet. Both sides are veneer
[0032] (4) Place the slab in a hard male and female mold made of "U"-shaped laminated wood, i...
PUM
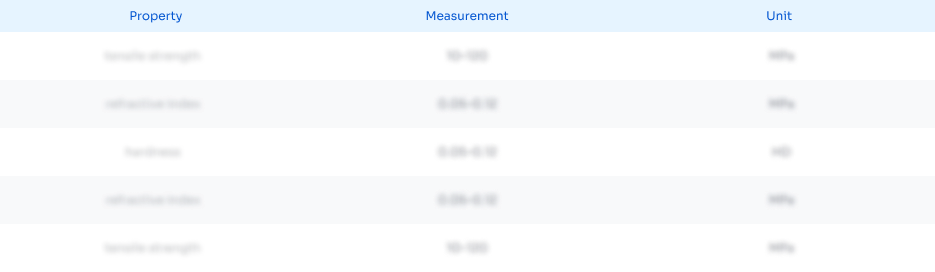
Abstract
Description
Claims
Application Information

- R&D Engineer
- R&D Manager
- IP Professional
- Industry Leading Data Capabilities
- Powerful AI technology
- Patent DNA Extraction
Browse by: Latest US Patents, China's latest patents, Technical Efficacy Thesaurus, Application Domain, Technology Topic, Popular Technical Reports.
© 2024 PatSnap. All rights reserved.Legal|Privacy policy|Modern Slavery Act Transparency Statement|Sitemap|About US| Contact US: help@patsnap.com