Process for preparing carbon black-loaded cobalt-zinc ferrite wave-absorbing material
A technology of wave absorbing material and process method, applied in metal material coating process, liquid chemical plating, coating and other directions, can solve the problem of easy agglomeration of nano ferrite, and achieve simple preparation process, easy process and easy operation. Effect
- Summary
- Abstract
- Description
- Claims
- Application Information
AI Technical Summary
Problems solved by technology
Method used
Image
Examples
Embodiment 1
[0023] (a), first prepare 1000ml, 10.2% mixed metal salt solution from the following components according to the following weight ratio: zinc nitrate, iron nitrate, cobalt nitrate=0.8:0.2:2 for later use; (b), take the above Put 50ml of the prepared metal salt solution in a small beaker, add conductive carbon black at a ratio of 1:1 by weight, ultrasonically for at least 1 hour to disperse the suspension evenly, then titrate the dispersed suspension with 8% sodium hydroxide , so that the pH value is greater than 10; (c), move all the suspension solution obtained in step (b) into a hydrothermal reaction kettle, and put the reaction kettle into an oven at 220°C for solvothermal reaction, and the reaction time is 8h; ( d) Cool naturally after the solvothermal reaction is completed, filter with Buchner funnel after cooling, wash with deionized water until neutral, and finally dry to obtain the finished product.
Embodiment 2
[0025] (a), first prepare 1000ml, 10.2% mixed metal salt solution from the following components according to the following weight ratio: zinc nitrate, iron nitrate, cobalt nitrate=0.8:0.2:2 for later use; (b), take the above Put 50ml of the prepared metal salt solution in a small beaker, add conductive carbon black at a ratio of 1:1 by weight, ultrasonically for at least 1 hour to disperse the suspension evenly, then titrate the dispersed suspension with 8% sodium hydroxide , so that the pH value is greater than 11; (c), move all the suspension solution obtained in step (b) into a hydrothermal reaction kettle, and put the reaction kettle into an oven at 200°C for solvothermal reaction, and the reaction time is 12h; ( d) Cool naturally after the solvothermal reaction is completed, filter with Buchner funnel after cooling, wash with deionized water until neutral, and finally dry to obtain the finished product.
Embodiment 3
[0027] (a), first prepare 1000ml, 10.2% mixed metal salt solution from the following components according to the following weight ratio: zinc nitrate, iron nitrate, cobalt nitrate=0.8:0.2:2 for later use; (b), take the above Put 50ml of the prepared metal salt solution in a small beaker, add conductive carbon black at a ratio of 1:1 by weight, ultrasonically for at least 1 hour to disperse the suspension evenly, then titrate the dispersed suspension with 8% sodium hydroxide , so that the pH value is greater than 11; (c), move all the suspension solution obtained in step (b) into a hydrothermal reaction kettle, and put the reaction kettle into an oven at 180°C for solvothermal reaction, and the reaction time is 16h; ( d) Cool naturally after the solvothermal reaction is completed, filter with Buchner funnel after cooling, wash with deionized water until neutral, and finally dry to obtain the finished product.
[0028] like figure 1 It is a scanning electron micrograph of the c...
PUM
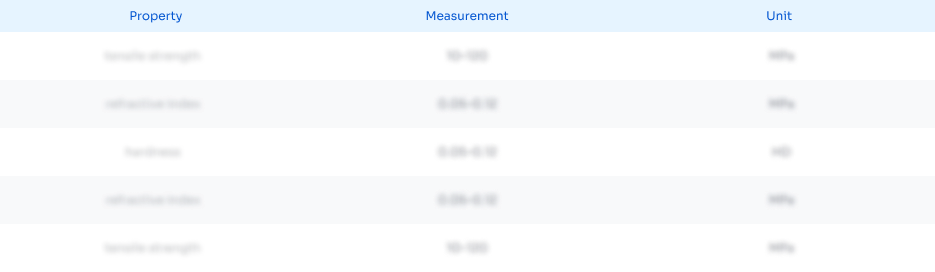
Abstract
Description
Claims
Application Information

- R&D
- Intellectual Property
- Life Sciences
- Materials
- Tech Scout
- Unparalleled Data Quality
- Higher Quality Content
- 60% Fewer Hallucinations
Browse by: Latest US Patents, China's latest patents, Technical Efficacy Thesaurus, Application Domain, Technology Topic, Popular Technical Reports.
© 2025 PatSnap. All rights reserved.Legal|Privacy policy|Modern Slavery Act Transparency Statement|Sitemap|About US| Contact US: help@patsnap.com