A kind of surface treatment copper foil and preparation method thereof
A surface treatment and copper foil technology, applied in the field of surface treatment copper foil and its preparation, can solve the problems of product quality and performance being difficult to meet use requirements, process parameters being difficult to accurately control, reducing copper foil quality and performance, etc. Controllable, easy to control operating conditions, low production efficiency
- Summary
- Abstract
- Description
- Claims
- Application Information
AI Technical Summary
Problems solved by technology
Method used
Image
Examples
Embodiment 1
[0032] No. 1 electro-cleaning solution was used, and the copper foil substrate was used as the cathode, and the copper foil substrate was electro-cleaned by brush plating for 30s under the conditions of a voltage of 14-18V, a temperature of 20°C, and a relative movement speed of 0.05m / s of the cathode and anode. , then washed with deionized water. Then use No. 3 activation solution, copper foil substrate as anode, brush plating for 30s under the conditions of voltage 14-18V, temperature 20°C, and relative movement speed of cathode and anode 0.05m / s, to activate the surface of copper foil substrate , then washed with deionized water. Then the composition is ZnSO 4 ·7H 2 O30g / l, NiSO 4 ·6H 2 O100g / l, C 6 H 8 O 7 ·H 2 O50g / l, CH 3 COONa40g / l, Na 2 SO 4 40g / l brush plating solution, brush plating for 90s under the conditions of voltage 14-18V, pH value 2, temperature 20°C, and relative motion speed of cathode and anode of 0.05m / s to obtain zinc-nickel alloy anti-diffusi...
Embodiment 2
[0034] Using No. 1 electrocleaning solution, copper foil substrate as cathode, brush plating for 10s under the conditions of voltage 6~10V, temperature 30°C, and relative movement speed of cathode and anode 0.4m / s, and electrocleaning copper foil substrate , then washed with deionized water. Then use No. 3 activation solution, copper foil substrate as anode, brush plating for 10s under the conditions of voltage 6-10V, temperature 30°C, and relative movement speed of cathode and anode 0.4m / s, to activate the surface of copper foil substrate , then washed with deionized water. Then the composition is ZnSO 4 ·7H 2 O30g / l, NiSO 4 ·6H 2 O25g / l, C 6 H 8 O 7 ·H 2 O65g / l, CH 3 COONa40g / l, Na 2 SO 4 40g / l brush plating solution, brush plating for 30s under the conditions of voltage 6-10V, pH value 3, temperature 30°C, and relative motion speed of cathode and anode 0.4m / s to obtain zinc-nickel alloy anti-diffusion barrier layer, Then wash with deionized water. Followed by t...
Embodiment 3
[0036] No. 1 electro-cleaning solution was used, and the copper foil substrate was used as the cathode, and the copper foil substrate was electro-cleaned by brush plating for 20s under the conditions of a voltage of 10-14V, a temperature of 20°C, and a relative motion speed of 0.2m / s between the cathode and anode. , then washed with deionized water. Then use No. 3 activation solution, copper foil substrate as anode, brush plating for 20s under the conditions of voltage 10-14V, temperature 20°C, and relative movement speed of cathode and anode 0.2m / s, to activate the surface of copper foil substrate , then washed with deionized water. Then the composition is ZnSO 4 ·7H 2 O30g / l, NiSO 4 ·6H 2 O60g / l, C 6 H 8 O 7 ·H 2 O30g / l, CH 3 COONa60g / l, Na 2 SO 4 40g / l brush plating solution, brush plating for 150s under the conditions of voltage 10-14V, pH value 4.5, temperature 20°C, and cathode and anode relative motion speed 0.2m / s, to obtain zinc-nickel alloy anti-diffusion ...
PUM
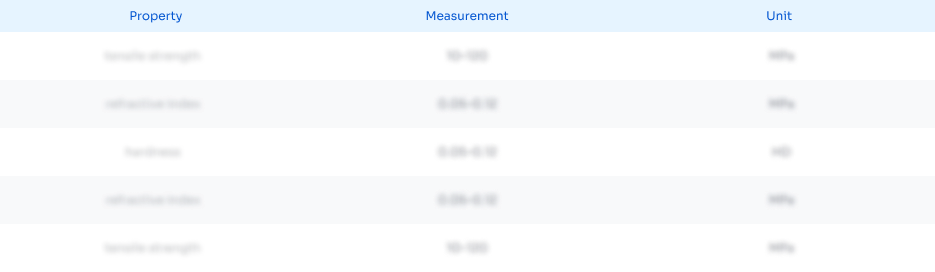
Abstract
Description
Claims
Application Information

- R&D
- Intellectual Property
- Life Sciences
- Materials
- Tech Scout
- Unparalleled Data Quality
- Higher Quality Content
- 60% Fewer Hallucinations
Browse by: Latest US Patents, China's latest patents, Technical Efficacy Thesaurus, Application Domain, Technology Topic, Popular Technical Reports.
© 2025 PatSnap. All rights reserved.Legal|Privacy policy|Modern Slavery Act Transparency Statement|Sitemap|About US| Contact US: help@patsnap.com