Low-loss MnZn ferrite material sintering method
A technology of ferrite material and sintering method, which is applied in the field of sintering of MnZn ferrite materials, can solve the problems of no sintering process research, etc., and achieve the effects of low sintering cost, long service life of kiln, and reduced loss
- Summary
- Abstract
- Description
- Claims
- Application Information
AI Technical Summary
Problems solved by technology
Method used
Examples
Embodiment 1
[0021] will consist of 52.6mol% Fe 2 o 3 , 12mol% ZnO, 35.4mol% MnO raw materials were mixed in a sand mill for 1 hour, and then pre-fired at 850 °C for 2 hours. Based on the mass of the pre-fired powder, add auxiliary components to the above-mentioned pre-fired material. The added auxiliary components (wt%) are: 0.1wt% CaCO 3 , 0.04wt% Nb 2 o 5 , 0.03wt% V 2 o 5 . Then carry out secondary sand grinding for 2 hours, spray granulation after adding PVA, and shape it into a standard annular magnetic core of Φ25 for sintering. In the sintering process, in the first heating stage, the stage is raised from room temperature to 700°C at a heating rate of 2°C / min, and the heating is carried out in the atmosphere; then from 700°C to 1200°C at a heating rate of 1.0 °C / min, the partial pressure of oxygen in this heating stage is maintained at 0.5%; in the second heating stage, this stage is raised from 1200°C to 1300°C, the heating rate is 5°C / min, and the partial pressure of oxyge...
Embodiment 2
[0026] will consist of 52.8mol% Fe 2 o 3 , 11mol% ZnO, 36.2mol% MnO raw materials were mixed in a sand mill for 1 hour, and then pre-fired at 900 °C for 2 hours. Based on the mass of the pre-fired powder, add auxiliary components to the above-mentioned pre-fired material. The added auxiliary components (wt%) are: 0.12wt% CaCO 3 , 0.02wt% V 2 o 5 , 0.04wt% ZrO 2 . Then carry out secondary sand grinding for 2 hours, spray granulation after adding PVA, and shape it into a standard annular magnetic core of Φ25 for sintering. In the sintering process, in the first heating stage, the stage is raised from room temperature to 700°C at a heating rate of 2°C / min, and the heating is carried out in the atmosphere; then from 700°C to 1200°C at a heating rate of 1.0 °C / min, the partial pressure of oxygen in this heating stage is maintained at 0.5%; in the second heating stage, this stage is raised from 1200°C to 1300°C, the heating rate is 5°C / min, and the partial pressure of oxygen i...
Embodiment 3
[0032] will consist of 53mol% Fe 2 o 3 , 10mol% ZnO, 37mol% MnO raw materials were mixed in a sand mill for 1 hour, and then pre-fired at 950 °C for 2 hours. Based on the mass of the pre-fired powder, add auxiliary components to the above-mentioned pre-fired material. The added auxiliary components (wt%) are: 0.08wt% CaCO 3 , 0.02wt% Nb 2 o 5 , 0.02wt% ZrO 2 . Then carry out secondary sand grinding for 2 hours, spray granulation after adding PVA, and shape it into a standard annular magnetic core of Φ25 for sintering. In the sintering process, in the first heating stage, the stage is raised from room temperature to 700°C at a heating rate of 2°C / min, and the heating is carried out in the atmosphere; then from 700°C to 1200°C at a heating rate of 1.0 °C / min, the oxygen partial pressure in this heating stage is maintained at 0.5%; in the second heating stage, this stage is raised from 1200°C to 1310°C, the heating rate is 5°C / min, and the oxygen partial pressure in the hea...
PUM
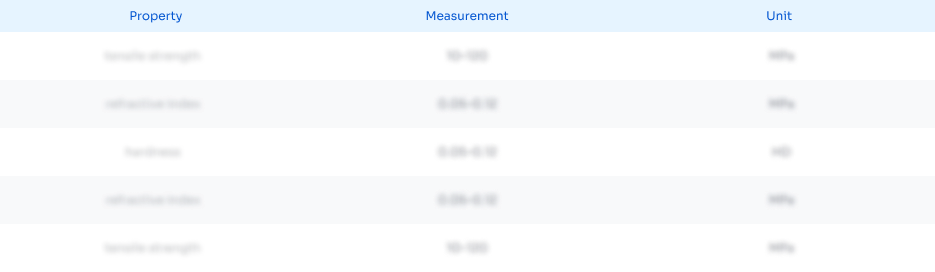
Abstract
Description
Claims
Application Information

- R&D
- Intellectual Property
- Life Sciences
- Materials
- Tech Scout
- Unparalleled Data Quality
- Higher Quality Content
- 60% Fewer Hallucinations
Browse by: Latest US Patents, China's latest patents, Technical Efficacy Thesaurus, Application Domain, Technology Topic, Popular Technical Reports.
© 2025 PatSnap. All rights reserved.Legal|Privacy policy|Modern Slavery Act Transparency Statement|Sitemap|About US| Contact US: help@patsnap.com