Assembling type floor formwork system with preset anchor nuts
A prefabricated and nut technology, which is applied in the treatment of formwork, formwork/formwork/work frame, and on-site preparation of building components, etc., can solve the problems of wasting labor, damage, and cannot be reused, and achieves easy turnover. Use and solve the effect of labor-intensive
- Summary
- Abstract
- Description
- Claims
- Application Information
AI Technical Summary
Problems solved by technology
Method used
Image
Examples
Embodiment Construction
[0029] The present invention will be further described below in conjunction with the accompanying drawings.
[0030] Such as Figure 1-6 As shown, a floor formwork support system with prefabricated anchor nuts, including: a steel truss 1, a formwork panel 2 and a fixed connection unit 3 for connecting the steel truss 1 and formwork panel 2, is characterized in that: The fixed connection unit 3 includes a lifting point nut 4 and a load-bearing screw 5, the lifting point nut 4 is fixedly connected to the main reinforcement of the lower chord of the steel bar truss 1, and the load-bearing screw 5 includes a screw 6 and a gasket 7. The screw rod 6 passes through the gasket 7, the template panel 2 and the concrete protective layer in turn and then screws into the lifting point nut 4, and the template panel 2 is provided with a plurality of through holes 8 for passing through the screw rod 6 .
[0031] The lifting point nut 4 is used to control the thickness of the concrete protec...
PUM
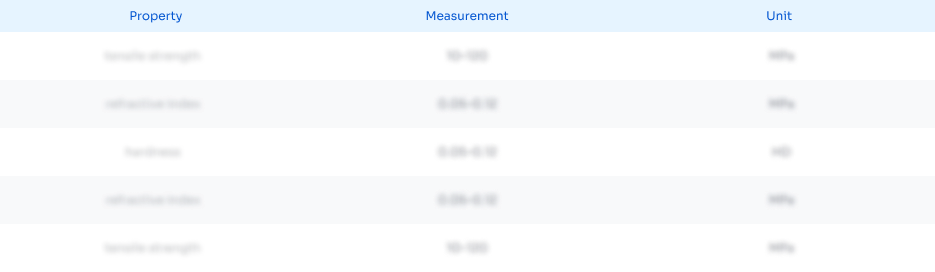
Abstract
Description
Claims
Application Information

- R&D
- Intellectual Property
- Life Sciences
- Materials
- Tech Scout
- Unparalleled Data Quality
- Higher Quality Content
- 60% Fewer Hallucinations
Browse by: Latest US Patents, China's latest patents, Technical Efficacy Thesaurus, Application Domain, Technology Topic, Popular Technical Reports.
© 2025 PatSnap. All rights reserved.Legal|Privacy policy|Modern Slavery Act Transparency Statement|Sitemap|About US| Contact US: help@patsnap.com