Method and equipment for treating oil stain and flue dust through flue gas desulfurization system
A desulfurization system and oil pollution technology, applied in separation methods, chemical instruments and methods, and separation of dispersed particles, can solve problems such as inability to solve absorption liquid separation and disposal, inability to handle slurry, etc., to achieve improved purification effect, improved adaptability, and stability quality effect
- Summary
- Abstract
- Description
- Claims
- Application Information
AI Technical Summary
Problems solved by technology
Method used
Image
Examples
Embodiment approach 1
[0029] Implementation Mode 1—Application when the boiler is fed with oil and ignited:
[0030]When the boiler is fueled and ignited, the boiler burns diesel to raise the temperature of the furnace to a certain temperature and then feeds coal. After the coal burns normally, it stops fueling. During this period, the flue gas contains a large amount of soot, coal powder, and smoke. There is no bypass for desulfurization, and the electrostatic precipitator cannot be used normally when oil is turned on and ignited. The flue gas containing oil and coal powder directly enters the desulfurization absorption tower. At this time, the flue gas has sulfur dioxide and needs to be desulfurized before it can be emptied. In order to ensure the safety of the absorption tower and perform desulfurization, the desulfurization absorption tower must be put into operation.
[0031] During the fuel injection and ignition of the boiler, the desulfurization absorption tower uses the original desulfuri...
Embodiment approach 2
[0033] Implementation Mode 2—Application of short-term failure of boiler dust collector:
[0034] When the dust collector of the boiler fails, the dust removal efficiency drops, the flue gas contains a lot of smoke and dust, the absorption liquid gradually turns gray from clean water, and the smoke and dust enter the absorption liquid. The pump sends the soot-containing absorption liquid in the maintenance pool to the filter for filtration (no need to enter the oil and dust separator). The filtrate is clean absorption liquid and returned to the absorption tower for use, and the filter residue is soot residue.
[0035] Operation effect: After the absorption liquid is polluted by smoke and dust when the dust collector suddenly fails, the entire desulfurization system continues to operate, maintaining normal desulfurization, flue gas discharge up to standard, and no waste water discharge, no secondary pollution. After the quality of the absorption liquid is stable, the absorption...
Embodiment approach 3
[0036] Implementation Mode Three - Application of Boiler Oven:
[0037] When the boiler is baked, the boiler burns heavy oil to raise the temperature of the furnace according to the requirements of the furnace curve. During the furnace, the amount of smoke is small but the smoke is black and contains a lot of oil fume. There is no bypass for desulfurization, and the electrostatic precipitator cannot be used during the oven, and the black oil fume directly enters the desulfurization absorption tower, and the temperature of the flue gas can reach up to 150°C, which exceeds the temperature resistance range of the absorption tower internals. In order to ensure the safety of the absorption tower, add water to the desulfurization absorption tower for circulation, and produce a large amount of black sewage containing oil and tar. After the oven is finished, the sewage in the absorption tower is discharged into the maintenance pool at one time through the circulation pump, and the main...
PUM
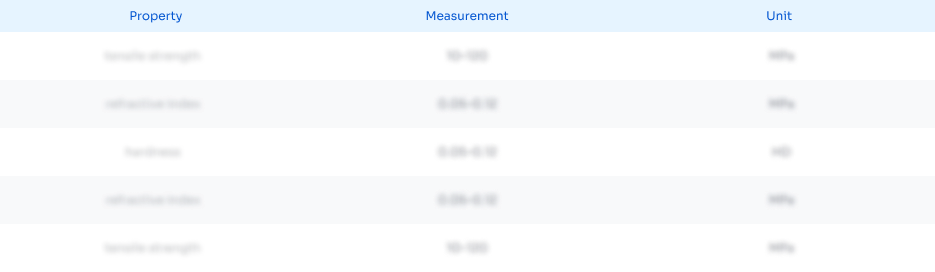
Abstract
Description
Claims
Application Information

- R&D
- Intellectual Property
- Life Sciences
- Materials
- Tech Scout
- Unparalleled Data Quality
- Higher Quality Content
- 60% Fewer Hallucinations
Browse by: Latest US Patents, China's latest patents, Technical Efficacy Thesaurus, Application Domain, Technology Topic, Popular Technical Reports.
© 2025 PatSnap. All rights reserved.Legal|Privacy policy|Modern Slavery Act Transparency Statement|Sitemap|About US| Contact US: help@patsnap.com