Ageing heat treatment process of 3003 aluminium alloy electronic foil
A technology of aging heat treatment and aluminum alloy, which is applied in the field of aging heat treatment process of 3003 aluminum alloy electronic foil, can solve the problem of not performing aging heat treatment, etc., and achieve the effect of improving specific capacitance and good corrosion effect.
- Summary
- Abstract
- Description
- Claims
- Application Information
AI Technical Summary
Problems solved by technology
Method used
Examples
Embodiment 1
[0012] Example 1 3003 hot-rolled billet plan:
[0013] 1) Hot rolled from hot rolled billet to , homogenizing annealing is performed at this thickness, and the annealing mechanism is .
[0014] 2) After four times of cold rolling (after the first pass of cold rolling is , after the second cold rolling pass is , after the third pass of cold rolling is , after the fourth pass of cold rolling is ) process, the thickness, carry out Fully annealed process.
[0015] 3) Continue cold rolling to , and then converted to foil rolling production, after three foil rollings (after the first foil rolling is , after the second foil rolling is , after the third foil rolling is ) process, the thickness, carry out Artificial aging.
[0016] 4) After three times of foil rolling (after the first foil rolling, , after the second foil rolling is , the third foil rolling can be selected to generate according to specific needs Aluminum foil with different thickness ...
Embodiment 2
[0020] Example 2 3003 casting and rolling billet plan:
[0021] 1) Hot rolled from cast billet to , homogenizing annealing is performed at this thickness to make the structure uniform and reduce segregation. The annealing mechanism is .
[0022] 2) After five passes of cold rolling (after the first pass of cold rolling is , after the second cold rolling pass is , after the third pass of cold rolling is , after the fourth pass of cold rolling is , after the fifth pass of cold rolling is ) process, the thickness, carry out Complete annealing process to reduce the residual stress of the tissue.
[0023] 3) Continue cold rolling to , and then converted to foil rolling production, after two foil rollings (after the first foil rolling is , after the second foil rolling is ) process, the thickness, carry out Artificial aging.
[0024] 4) After three times of foil rolling (after the first foil rolling, , after the second foil rolling is , the third foil...
PUM
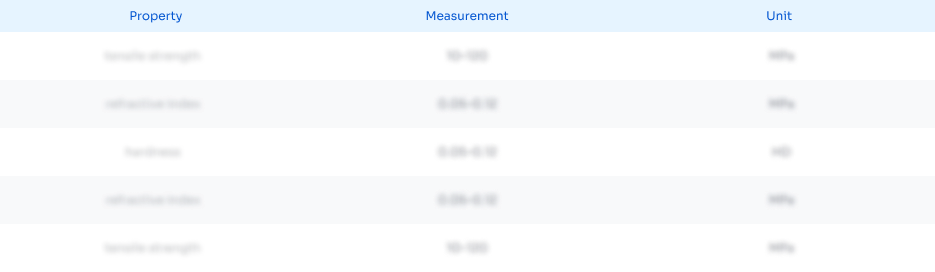
Abstract
Description
Claims
Application Information

- R&D
- Intellectual Property
- Life Sciences
- Materials
- Tech Scout
- Unparalleled Data Quality
- Higher Quality Content
- 60% Fewer Hallucinations
Browse by: Latest US Patents, China's latest patents, Technical Efficacy Thesaurus, Application Domain, Technology Topic, Popular Technical Reports.
© 2025 PatSnap. All rights reserved.Legal|Privacy policy|Modern Slavery Act Transparency Statement|Sitemap|About US| Contact US: help@patsnap.com