Preparation method of anti-carbon deposition and anti-sintering monolithic methane dry reforming catalyst
A monolithic catalyst, methane dry reforming technology, applied in chemical instruments and methods, physical/chemical process catalysts, metal/metal oxide/metal hydroxide catalysts, etc., can solve the problem of uneven distribution of active components, easy Carbon deposition activity degradation, cumbersome preparation steps and other problems, to achieve good anti-carbon deposition and anti-Ni particle sintering performance, is conducive to catalyzing methane dry reforming reaction, and improve the effect of specific surface area
- Summary
- Abstract
- Description
- Claims
- Application Information
AI Technical Summary
Problems solved by technology
Method used
Image
Examples
Embodiment 1
[0020] First remove the surface oxides of the metal wire mesh in dilute acid, and then ultrasonically treat it in ethanol and water respectively;
[0021] Put the wire mesh into 0.04 mol / L Ni(NO 3 ) 2 , 0.10 mol / L Mg(NO 3 ) 2 and 1.0 mol / L NH 4 In the mixed solution of Cl, the pH value was adjusted to 6.5 with 1 wt% ammonia solution. All transferred to a Teflon-lined autoclave, 150 o C water for 12 h. In situ growth to obtain the multi-component metal hydroxide film wire mesh with absolute ethanol, drying. The resulting barbed wire was heated in a tube furnace from room temperature to 600 o C, calcined for 4 h at 10 mol% H 2 content of H 2 and N 2 700 in the mixture o C was reduced for 1 h to obtain the final product. from figure 1 It can be seen that the surface of the catalyst obtained after calcination is a dense sheet-like array, and the Ni particles are uniformly dispersed on the nanosheets.
[0022] The method for the catalyst methane dry reforming test is:...
Embodiment 2
[0024] First remove the surface oxides of the metal aluminum wire mesh in dilute alkali, and then ultrasonically treat it in ethanol and water respectively;
[0025] Put the aluminum wire mesh into 0.1mol / L Ni(NO 3 ) 2 , 2 mol / L Mg(NO 3 ) 2 and 6.0 mol / L NH 4 In the mixed solution of Cl, the pH value was adjusted to 6.5 with 1 wt% ammonia solution. All transferred to a Teflon-lined autoclave, 120 o C water for 24 h. The aluminum wire mesh of the multi-component metal hydroxide film obtained by in-situ growth was dried with absolute ethanol. The resulting aluminum wire mesh was heated in a tube furnace from room temperature to 700 o C, calcined for 2 h at 10 mol% H 2 content of H 2 and N 2 650 in mixture o C was reduced for 2 h to obtain the final product.
[0026] The test conditions are the same as in Example 1, at a reaction temperature of 750 o C, measured CH 4 and CO 2 The conversion rate is over 85%. Compared with the traditional magnesium-aluminum mixed o...
Embodiment 3
[0028] First remove the surface oxides of the metal stainless steel wire mesh in dilute acid, and then ultrasonically treat it in ethanol and water respectively;
[0029] Put stainless steel wire mesh into 3 mol / L Ni(NO 3 ) 2 , 8 mol / L Mg(NO 3 ) 2 and 10.0 mol / L NH 4In the mixed solution of Cl, the pH value was adjusted to 6.5 with 1 wt% ammonia solution. All were transferred to a Teflon-lined autoclave, 200 o C water for 8 h. The stainless steel wire mesh obtained by in-situ growth of the multi-component metal hydroxide film was dried with absolute ethanol. The resulting stainless steel wire mesh was heated in a tube furnace from room temperature to 550 o C, calcined for 6 h at 10 mol% H 2 content of H 2 and N 2 750 in mixture o C was reduced for 1.5 h to obtain the final product.
[0030] The test conditions are the same as in Example 1, at a reaction temperature of 750 o C, measured CH 4 and CO 2 The conversion rate is over 85%. Compared with the traditiona...
PUM
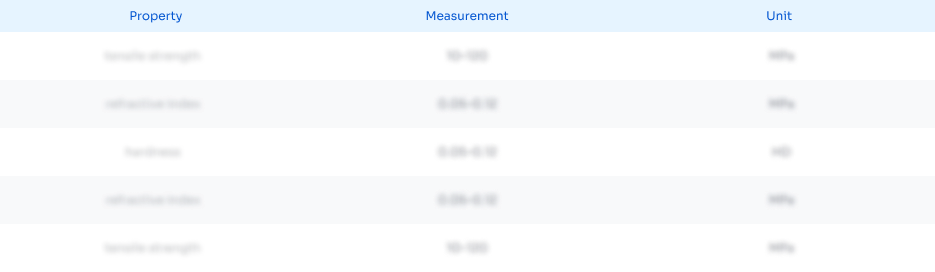
Abstract
Description
Claims
Application Information

- Generate Ideas
- Intellectual Property
- Life Sciences
- Materials
- Tech Scout
- Unparalleled Data Quality
- Higher Quality Content
- 60% Fewer Hallucinations
Browse by: Latest US Patents, China's latest patents, Technical Efficacy Thesaurus, Application Domain, Technology Topic, Popular Technical Reports.
© 2025 PatSnap. All rights reserved.Legal|Privacy policy|Modern Slavery Act Transparency Statement|Sitemap|About US| Contact US: help@patsnap.com