Operation method of electrostatic field oil-water separation system
A technology of oil-water separation and operation method, which is applied in the direction of electric liquid separation, etc., which can solve the problems of increased operation and maintenance costs, increased floor space, and high environmental protection pressure, so as to reduce sewage treatment costs and environmental protection pressure, and reduce operating costs. Maintenance cost and the effect of reducing the height of the emulsified layer
- Summary
- Abstract
- Description
- Claims
- Application Information
AI Technical Summary
Problems solved by technology
Method used
Image
Examples
Embodiment 1
[0028] The degassed well fluid enters the oil-water separation tank 1 from the degassed oil liquid input port 5. When the degassed well fluid in the oil-water separation tank 1 reaches the set standard, the valve of the degassed oil liquid input port 5 is closed, and the oil, water, Oil sludge is preliminarily separated by sedimentation, and the pressure machine 3 is opened to increase the air pressure in the oil-water separation tank 1. Under the action of pressure, oil, water, and oil sludge are further separated.
Embodiment 2
[0030] The control box 16 adjusts the voltage to the transformer 4, and outputs the voltage to the positive electrode plate 6 and the negative electrode ring electrode plate 7 through the wires, so that an electrostatic field space is formed between the positive electrode plate 6 and the negative electrode ring electrode plate 7, and the positive electrode plate Oil is separated from water within the electrostatic field of plate 6 and negative ring electrode plate 7 .
Embodiment 3
[0032] The upper pressure sensor 10 measures the upper pressure value in the oil-water separation tank 1, the lower pressure sensor 14 measures the lower pressure value in the oil-water separation tank 1, the upper pressure value and the lower pressure value are transmitted to the adapter module 17 through wires, and the adapter module 17 After the pressure value signal is converted, it is input to the central computer 18, and the central computer 18 calculates the pressure difference between the upper and lower sides of the oil-water separation tank 1, and obtains the position of the oil-water interface in the oil-water separation tank 1, and adjusts the pressure machine 3 so that the oil-water interface is located in the electrostatic field space of the middle.
PUM
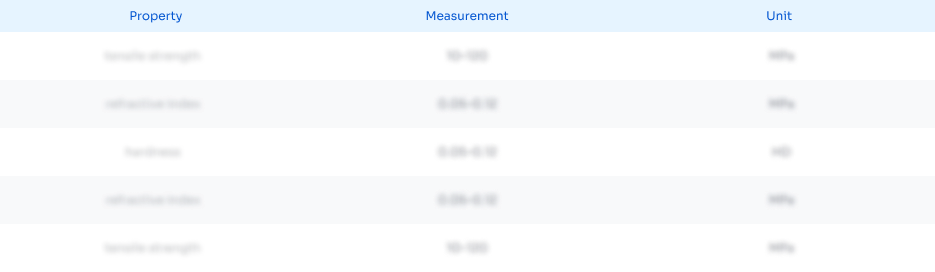
Abstract
Description
Claims
Application Information

- Generate Ideas
- Intellectual Property
- Life Sciences
- Materials
- Tech Scout
- Unparalleled Data Quality
- Higher Quality Content
- 60% Fewer Hallucinations
Browse by: Latest US Patents, China's latest patents, Technical Efficacy Thesaurus, Application Domain, Technology Topic, Popular Technical Reports.
© 2025 PatSnap. All rights reserved.Legal|Privacy policy|Modern Slavery Act Transparency Statement|Sitemap|About US| Contact US: help@patsnap.com