Method for preparing ethylene and propylene by taking naphtha as raw material
A technology of ethylene propylene and naphtha, which is applied in the production of bulk chemicals, chemical instruments and methods, and molecular sieve catalysts. High material conversion rate and product yield, optimized catalytic reaction process, and uniform bed temperature distribution
- Summary
- Abstract
- Description
- Claims
- Application Information
AI Technical Summary
Problems solved by technology
Method used
Image
Examples
Embodiment 1
[0025] A method for producing ethylene propylene with naphtha as a raw material, comprising the steps of:
[0026] (1) Preparation of composite catalyst: Mix the weighed ZSM-5 molecular sieve, RE-USY molecular sieve, binder, and distilled water evenly, then crystallize, filter, wash, dry, and roast to obtain a composite catalyst, in which ZSM-5 The weight ratio of molecular sieve to RE-USY molecular sieve is 2:1;
[0027] (2) Catalytic cracking: deionized water and naphtha are fed into the raw material preheating gasifier through metering pumps respectively, and preheated gasification is carried out at 210°C, and then the gasified deionized water and naphtha are Enter the reactor from the bottom of the fixed fluidized bed reactor for catalytic cracking reaction, wherein the catalyst load is 3g naphtha / g catalyst hour, the weight ratio of deionized water to naphtha is 2:1, and the reaction temperature is 630°C, reaction pressure 0.08MPa, reaction mass space velocity 2 hours -...
Embodiment 2
[0038] A method for producing ethylene propylene with naphtha as a raw material, comprising the steps of:
[0039] (1) Preparation of composite catalyst: Mix the weighed ZSM-5 molecular sieve, RE-USY molecular sieve, binder, and distilled water evenly, then crystallize, filter, wash, dry, and roast to obtain a composite catalyst, in which ZSM-5 The weight ratio of molecular sieve to RE-USY molecular sieve is 1:1;
[0040] (2) Catalytic cracking: deionized water and naphtha are fed into the raw material preheating gasifier through metering pumps respectively, and preheated gasification is carried out at 230°C, and then the gasified deionized water and naphtha Enter the reactor from the bottom of the fixed fluidized bed reactor for catalytic cracking reaction, wherein the catalyst load is 5g naphtha / g catalyst hour, the weight ratio of deionized water to naphtha is 3:1, and the reaction temperature is 650°C, reaction pressure 0.5MPa, reaction mass space velocity 1 hour -1 ;
...
Embodiment 3
[0052] A method for producing ethylene propylene with naphtha as a raw material, comprising the steps of:
[0053] (1) Preparation of composite catalyst: Mix the weighed ZSM-5 molecular sieve, RE-USY molecular sieve, binder, and distilled water evenly, then crystallize, filter, wash, dry, and roast to obtain a composite catalyst, in which ZSM-5 The weight ratio of molecular sieve to RE-USY molecular sieve is 3:1;
[0054] (2) Catalytic cracking: deionized water and naphtha are fed into the raw material preheating gasifier through metering pumps respectively, and preheated gasification is carried out at 230°C, and then the gasified deionized water and naphtha Enter the reactor from the bottom of the fixed fluidized bed reactor for catalytic cracking reaction, wherein the catalyst load is 3g naphtha / g catalyst hour, the weight ratio of deionized water to naphtha is 1:1, and the reaction temperature is 680°C, reaction pressure 0.5MPa, reaction mass space velocity 2 hours -1 ; ...
PUM
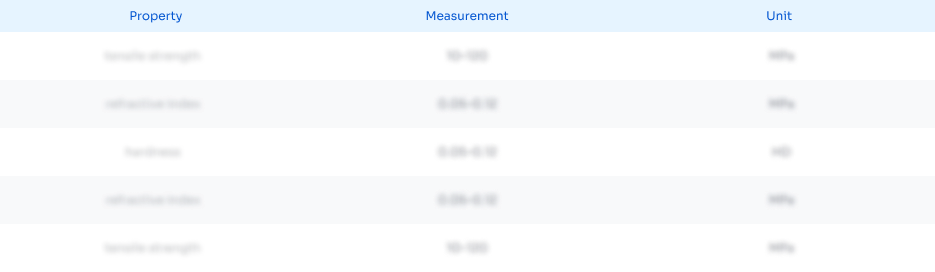
Abstract
Description
Claims
Application Information

- R&D
- Intellectual Property
- Life Sciences
- Materials
- Tech Scout
- Unparalleled Data Quality
- Higher Quality Content
- 60% Fewer Hallucinations
Browse by: Latest US Patents, China's latest patents, Technical Efficacy Thesaurus, Application Domain, Technology Topic, Popular Technical Reports.
© 2025 PatSnap. All rights reserved.Legal|Privacy policy|Modern Slavery Act Transparency Statement|Sitemap|About US| Contact US: help@patsnap.com