Control method for brushed direct current motor of electric running machine
A technology with a brushed DC motor and a control method, which is applied to sports accessories, training equipment for adjusting coordination, training equipment for adjusting the cardiovascular system, etc., can solve problems such as troublesome installation and maintenance, and achieve the effect of avoiding troublesome installation and maintenance
- Summary
- Abstract
- Description
- Claims
- Application Information
AI Technical Summary
Problems solved by technology
Method used
Image
Examples
Embodiment Construction
[0020] Such as figure 1 The schematic diagram of the voltage negative feedback current compensation speed control system is shown, and the current positive feedback signal is taken out through the sampling resistor Rs, where I d R s The polarity of the speed given signal U n The polarity is the same, and with the voltage negative feedback signal γU d opposite in polarity. u d is the armature terminal voltage. At the input of the operational amplifier, the speed given signal U n and the input loop resistance of the voltage negative feedback are both R 0 , the resistance of the current positive feedback input loop is R 2 , in order to obtain an appropriate current feedback coefficient β. When the load increases and the static speed drop increases, the current positive feedback signal also increases, and the voltage of the power electronic converter UPE increases through the operational amplifier, thereby compensating for the drop in speed. The specific current compensat...
PUM
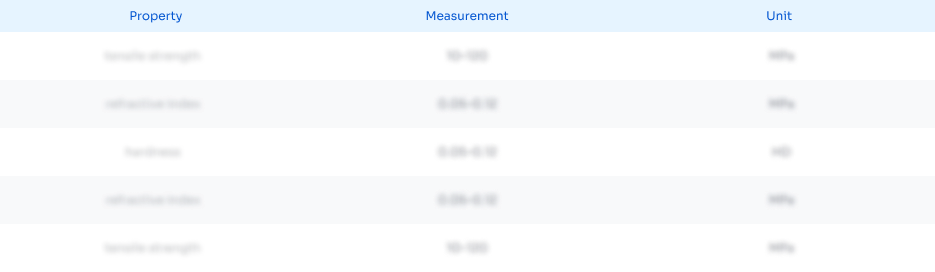
Abstract
Description
Claims
Application Information

- Generate Ideas
- Intellectual Property
- Life Sciences
- Materials
- Tech Scout
- Unparalleled Data Quality
- Higher Quality Content
- 60% Fewer Hallucinations
Browse by: Latest US Patents, China's latest patents, Technical Efficacy Thesaurus, Application Domain, Technology Topic, Popular Technical Reports.
© 2025 PatSnap. All rights reserved.Legal|Privacy policy|Modern Slavery Act Transparency Statement|Sitemap|About US| Contact US: help@patsnap.com