Buried steel pipeline coating stripping and corrosion test system under stress and stray current coupling effect
A stray current, corrosion test technology, applied in the direction of weather resistance/light resistance/corrosion resistance, measuring devices, instruments, etc., can solve problems such as single function, inability to simulate the actual working conditions of buried pipelines, and inability to combine organically.
- Summary
- Abstract
- Description
- Claims
- Application Information
AI Technical Summary
Problems solved by technology
Method used
Image
Examples
Embodiment Construction
[0025] exist figure 1 As shown in the specific structural cross-sectional view of a buried steel pipeline coating stripping and corrosion test system of the present invention under the coupled action of stress and stray current, silicone oil is poured into the pipeline 14 to build a stress loading test system. Push the force application handle 1 to drive the loading screw 2 to rotate through the screw drive to generate an axial force to compress the coil spring 9 and then transmit the force to the piston 12. The piston 12 compresses the silicone oil to generate pressure so that the pipeline 14 is subjected to stress. Observe the pressure gauge 19. Stop pushing the force-applying handle 1 until the specified pressure, and tighten the bolt 8 to prevent the loading screw 2 from rotating. When the stress on the pipeline 14 needs to be changed, the bolt 8 is unscrewed, and the force application handle 1 is pushed until the required pressure is reached, and then the bolt 8 is tighte...
PUM
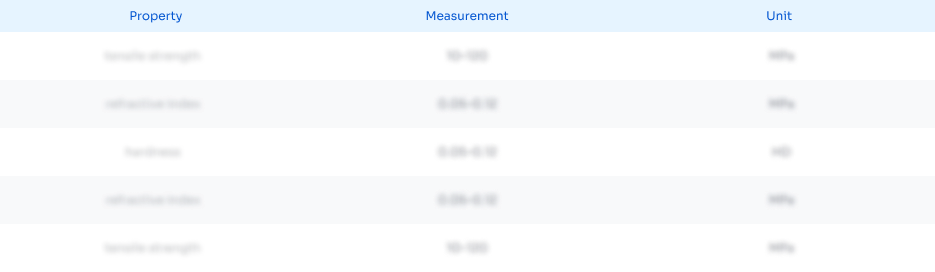
Abstract
Description
Claims
Application Information

- R&D
- Intellectual Property
- Life Sciences
- Materials
- Tech Scout
- Unparalleled Data Quality
- Higher Quality Content
- 60% Fewer Hallucinations
Browse by: Latest US Patents, China's latest patents, Technical Efficacy Thesaurus, Application Domain, Technology Topic, Popular Technical Reports.
© 2025 PatSnap. All rights reserved.Legal|Privacy policy|Modern Slavery Act Transparency Statement|Sitemap|About US| Contact US: help@patsnap.com