Fast calibration method of multiple line structured light visual sensor
A visual sensor and multi-line structured light technology, applied in the field of visual inspection, can solve problems such as complex methods, light strip matching, and low efficiency
- Summary
- Abstract
- Description
- Claims
- Application Information
AI Technical Summary
Problems solved by technology
Method used
Image
Examples
Embodiment Construction
[0060] In order to make full use of the characteristics of multi-line structured light, the present invention refers to the Zhang camera calibration process, and uses the plane target to place multiple non-coplanar positions to obtain the virtual space feature point array on each light plane for system calibration. A fast calibration method of multi-line structured light vision sensor based on directional planar grid target is proposed, which can quickly and conveniently complete the accurate calibration of multi-line structured light, and is suitable for on-site calibration.
[0061] The present invention comprises the steps:
[0062] 1. Measurement model
[0063] The schematic diagram of the measurement model of the multi-line structured light vision sensor established in this design scheme is as follows: figure 1 shown. The system measurement coordinate system Os-XsYsZs is directly established on the world coordinate system Ow-XwYwZw determined by the placement position ...
PUM
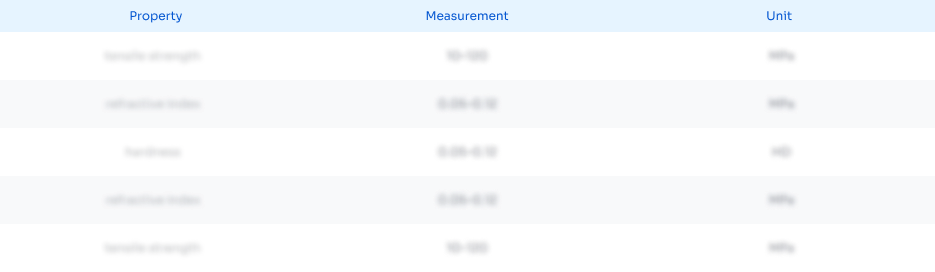
Abstract
Description
Claims
Application Information

- R&D
- Intellectual Property
- Life Sciences
- Materials
- Tech Scout
- Unparalleled Data Quality
- Higher Quality Content
- 60% Fewer Hallucinations
Browse by: Latest US Patents, China's latest patents, Technical Efficacy Thesaurus, Application Domain, Technology Topic, Popular Technical Reports.
© 2025 PatSnap. All rights reserved.Legal|Privacy policy|Modern Slavery Act Transparency Statement|Sitemap|About US| Contact US: help@patsnap.com